Issue:October 2017
ADVANCED DELIVERY DEVICES - The Staked Needle Pre-Filled Syringe: Benefits, Conventional Limitations & a New Approach
introduction
In the world of subcutaneous and intramuscular injectable drug delivery, injection devices such as autoinjectors and wearable pumps are receiving a lot of attention. However, the importance of the Pre-Filled Syringe, both as a standalone device and as a sub-system within other injection devices, remains extremely high. Well understood benefits continue to drive the transition from vials to Pre-Filled Syringes as the preferred approach for injectable drugs. These benefits include user convenience, reduced risk of contamination, reduction on overfill requirements, and compatibility with safety devices and autoinjectors. A syringe with a pre-attached needle brings further advantages, but the current approach to forming a Staked Needle Syringe presents inherent risks stemming from the use of glue as the needle attachment mechanism. A new approach that addresses these challenges inherent in the conventional approach presents an important alternative to the current standard.
STAKED & LUER PRE-FILLED SYRINGES
With pre-filled syringes, liquid drug formulations are commonly stored for a shelf-life of up to 3 years. Two main categories of syringes can be found; the Staked (or Pre-Attached) Needle Syringe in which the injection cannula is already pre-attached, and the Luer Cone/Luer Lock Syringes in which the user attaches a hypodermic needle at the time of injection. The Luer Lock type differs from the Luer Cone due to the presence of a groove on the neck for snap-fit components, such as Luer Lock Adapters. Each type of syringe also has various options for the proximal flange: the large and small round flange as well as the cut flange, which has the advantage of preventing the syringe from rolling during injection preparation. These syringes are described in detail in the ISO 11040-4 Standard.1 Depending on the route of administration, certain needle geometries are typically used as seen in Table 1.
An obvious but very important difference between the Staked and Luer Syringe is that the Luer Syringe requires the user to mount a needle prior to injection. This brings with it the freedom to choose the correct needle to deliver the drug to the appropriate depth for a specific patient and/or injection site. For example, a user will choose a longer needle for an IM Injection into an obese patient or for a gluteal injection, as compared to a shorter needle for a thinner patient or a deltoid injection. However, the needle-choice flexibility that a Luer Syringe provides brings with it some usability disadvantages and risk for error. The user must first choose the correct needle length and gauge and then properly attach the needle. These additional steps are inconvenient and take additional time, but more importantly, they leave the user prone to impactful error; the incorrect needle can lead to a misplaced deposit of the medication, while an improperly attached needle can lead to leaking and inaccurate dosing.
THE STAKED NEEDLE: BENEFITS & CONVENTIONAL APPROACH TO PRODUCTION
The Staked Needle emerged as an effective means of avoiding these risks by eliminating the requirement for additional user steps. While risk mitigation was the main driver, further benefits that accompanied the Staked Needle were improved handling, reduced risk of contamination, enhanced user convenience, as well as reduced time of administration. These factors have propelled the Staked Needle Syringe to cover a significant market share within the Pre-Filled Syringe industry, particularly in therapeutic areas, such as heparins, certain vaccines, and biologics.
Glass Pre-Filled Syringes are manufactured from glass tubes of a predetermined inner and outer diameter. The tube is either pre-cut before forming on horizontal machines or directly formed out of the tube on vertical machines. Figure 1 shows a typical layout for vertical forming. Such lines consist of tubing loaders, hot forming units, visual inspection machines, reject stations, a furnace, and in the case of a Staked Needle Syringe, a needle bonding machine.
In the conventional approach to a Staked Needle, the stainless steel cannula is bonded into the needle channel of the syringe barrel using a UV-cured adhesive. This process occurs in the needle bonding machine depicted in Figure 1. This has been the industry’s approach to pre-attaching a needle to a glass syringe for many years. The complexity and cost associated with changing and validating this needle bonding process results in a limited array of needle gauge and length offerings in a Staked Needle presentation. After bonding and curing, the syringes are washed and siliconized, closed with either a soft or rigid needle shield, nested, tubbed, bagged, and ETO sterilized. They are then shipped to the customer, ready for aseptic filling.
LIMITATIONS OF CONVENTIONAL STAKED NEEDLE SYRINGES
Staked Needle Syringes have advantage compared to Luer Cone or Luer Lock Syringes as described previously, but they also have challenges and risks stemming from components that come into direct contact with the drug during long-term storage.
A Tungsten pin is used to form the fluid path in the cone of a glass, pre-filled syringe during syringe forming. UV-cured glue is then used to bond the needle to the glass. In the X-ray image in Figure 2 the red circle highlights the area where glue is present at the cone outlet and between the needle and the needle channel in the glass. The presence of glue introduces the risk for interaction of the drug with the adhesive and/or interaction with components of the adhesive that may be extracted. Leachables coming from the glue and/or closure system as well as residual tungsten oxides left behind from the tungsten pin can present a drug safety and efficacy risk. As an example, incomplete UV curing of the adhesive was found to cause unexpected impurities in a new staked needle Pre-filled Syringe presentation for a biological product, while this had not been previously observed in a Luer Cone presentation.2 Additionally, tungsten residues in the glass syringe cone left behind during manufacturing have led to aggregation and particle formation in protein solutions.3
Knowing these phenomena exist, it is common practice to set a specification for allowed tungsten levels and limits to non-cured glue monomers to lower the risks as much as possible. Because tungsten is known to interfere with some drugs, there are two options available for risk mitigation. Either the residual tungsten is controlled to a level that does not react with the drug product or another pin material is used to avoid the presence of tungsten oxides. This second approach risks that the alternative pin material may also interfere with the drug or that the pins may be quite costly.
Another area of discussion and research related to Pre-Filled Syringes is the amount of silicone oil used to allow for syringe lubrication and easy passage of the plunger stopper down the barrel of the syringe. The silicone is applied by spraying silicone oil onto the glass or by coating the glass with a silicone emulsion that is baked onto the glass. The goal for Biotech Syringes for Biologics is to lower the amount of silicone oil inside the syringe, which is intended to address the concerns of particulates and interaction between the silicone oil and drug product. Typically, “medical-grade” silicone oils are used for the lubrication of the inner syringe barrel as well as for the needle itself.4,5 Still, silicone can interact with proteins and lead to aggregation or silicone can be detected as particulates during particle testing. An alternative to the standard lubrication of the inner syringe barrel with pure silicone oil is a silicone emulsion that is baked at approximately 330°C for 20 to 30 mins. This process removes the water and causes a thin layer of silicone to chemically bind with the glass. The goal of this baked-on siliconization process is to reduce the chance of silicone reacting with proteins and leading to aggregation. This advanced process, however, is not compatible with standard glue-bonded Staked Syringes because the siliconization/baking process occurs after the needle-bonding process. Adhesive will not survive this baking temperature and, therefore, no baked silicone Staked Needle Syringes are commercially available on the market today. This is a significant and somewhat ironic limitation given that biologic drugs, which can benefit the most from the baked silicone process due to their sensitivity to silicone interaction, are often delivered subcutaneously and therefore lend themselves to a Staked Needle Syringe.
Staked Needle and Luer Needle Syringes each have their advantages and disadvantages and clearly play a significant role in drug delivery. Therefore, there are many new developments around Pre-Filled Syringe Systems with the goal of minimizing the limitations. For example, composite polymer Pre-Filled Syringes play an emerging role. General advantages of polymer syringes compared to glass are the higher break resistance, low leachable profiles from heavy metals, and the elimination of glue and tungsten because the needle is affixed with an “insert molding” process. Polymer syringes therefore address many of the risks inherent in glass Staked Needle Syringes, yet despite these advantages, glass Pre-Filled Syringes dominate the market. This may be because they are a known entity with a long history and a very well-known production process, from the tubing to the forming to the fill-finishing. The ideal solution, then, might be a system that preserves as many as possible of the existing components, equipment and processes the industry trusts, while avoiding as much as possible the interaction between the drug and the unwanted components. An additional element of the ideal solution would be combining this “dry needle system” with the integrated needle safety and reuse prevention elements that are required for Staked Needle Syringes in regulated environments. The Credence Companion® Staked Needle Syringe may offer such an approach.
THE COMPANION® STAKED NEEDLE SYRINGE
Credence MedSystems is built upon its commitment to offering the pharmaceutical industry Innovation Without Change. Credence’s product design and business model are focused on maximizing the impact of its innovative drug delivery systems while minimizing the disruption to pharmaceutical manufacturers during implementation. Pharmaceutical manufacturers can drive growth, brand differentiation, and loyalty by impressing their customers with the usability and protection offered by Credence’s novel injection devices, while preserving their established processes and supply chain preferences.
Credence’s approach allows pharmaceutical manufacturers to choose their preferred primary syringe container and closure components from their preferred suppliers. The Companion needle and plunger rod are incorporated with the preferred components to result in a fully integrated syringe system with passive needle-retraction safety. It is the mechanism by which Credence’s needle is attached to an existing syringe barrel that addresses the challenges presented by the conventional approach of gluing in a staked needle (Figure 3).
The Companion needle assembly includes a polymer hub that incorporates the following components: a needle and needle shield; piercing elements used for Credence’s needle retraction technology; and a seal that is integral to maintaining container closure. A standard Needle Shield is used to cover the needle. The manufacturing process that assembles the needle system allows flexibility to incorporate a wide variety of needle gauges and lengths, offering pharmaceutical manufacturers the ability to bring Staked Needle Syringes to a larger number of drug products. The Credence needle assembly is secured to a standard, commercially available Luer Cone Syringe barrel by mechanically attaching to the groove typically used for Luer Lock Adapters, tip caps, and other closure devices. This process occurs at the syringe manufacturer during syringe assembly so that the syringes are delivered to the filling lines pre-sterilized in the standard nest and tub configuration. The result is a system with the potential to set a new standard for Staked Needle Syringes. It preserves the use of existing syringe barrels, components, and processes, and has all the benefits of a pre-attached needle, but it eliminates the glue and thereby solves a challenge that has plagued the industry.
These significant advantages protect the safety of the patient by maintaining the integrity of the drug product. Removing the glue eliminates risk of unwanted interaction with the drug product, removes the requirement for specifications on the limit of non-cured monomers, and enables baked-on siliconization for a Staked Needle Syringe. Additionally, the system provides many important benefits to usability and user safety. The syringe has the familiar look and feel of conventional syringes, providing the user a level of comfort and allowing standard syringe operations, such as aspiration and air bubble removal. Drug product inspection is now simplified due to the unencumbered barrel. The user completes the injection and receives audible, visual, and tactile cues that the full dose has been delivered. Simultaneously, the needle automatically retracts through the stopper and into the barrel of the syringe, rendering the syringe needle-free and preventing reuse (Figure 4). These features help promote the successful delivery of the drug and drive compliance, while safeguarding the healthcare professionals, patients, and self-injectors using it.
FINAL THOUGHTS
The advantages of a Staked Needle Pre-Filled Syringe are clear and well documented, but significant risks remain due to the glued-in mechanism of needle attachment. Human nature can prevent us from addressing a problem until a potential solution is within reach, and therefore, the industry has coped with what was available. A new alternative is now available that not only addresses the known challenges, but adds critical usability and safety features while preserving existing components and processes. When new technology eliminates “necessary evils,” the technology should be explored for its potential to emerge as a new standard of care.
REFERENCES
1. ISO 11040-4 Prefilled Syringes – part 4: Glass barrels for injectables and subassembled sterilized syringes ready for filling (current version).
2. Adler M. Challenges in development of pre-filled syringes for biologics – a formulation scientist‘s point of view. Presented at the 2011 PDA Europe The Universe of Prefilled Syringes and Injection Devices, Basel, Switzerland, November 7-11, 2011.
3. Sacha GJ. Rogers A , Miller RL. Pre-filled syringes: a review of the history, manufacturing and challenges. Pharmaceut Develop Technol. 2015;20(1): 1-11.
4. USP Dimethicone (current version).
5. Pharm Eu. 3.1.8 Silicone oil used for lubricants (current version).
To view this issue and all back issues online, please visit www.drug-dev.com.
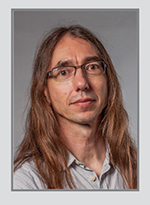
Horst Koller is CEO of HK Packaging Consulting GmbH. Prior to becoming a consultant, he worked for Abbott Diagnostic and SCHOTT Pharmaceutical Packaging with a total of more than 20 years industry experience. His consulting company is focussing on Technical, Regulatory, and QM-Support around Primary and Secondary Packaging Systems, including Medical Devices. He is an active member within the technical ISO Committees TC76 and TC84 as well as an active speaker at international conferences. He earned his Engineering degree in Biotechnology from the University of Applied Sciences in Mannheim, Germany.
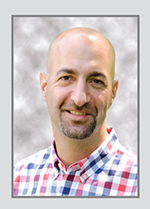
John A. Merhige is Chief Commercial Officer at Credence MedSystems, leading the company’s business development, sales, and marketing strategies. Previously, he was Vice President, Market Development at Sanofi BioSurgery, which he joined upon its acquisition of Pluromed, where he was a member of the Executive Management team. Mr. Merhige also founded Prelude Devices to identify and grow early stage medical technology ventures. He graduated from Dartmouth College with a Mechanical Engineering degree and returned to Dartmouth for a Masters in Engineering Management from the Thayer School of Engineering and the Tuck School of Business.
Total Page Views: 21814