Issue:January/February 2022
COATING TECHNOLOGY- Combining a State-of-the-Art Bromobutyl Formulation With a Proven ETFE Film for Exceptional Chemical Performance
INTRODUCTION
When developing a new drug product, a generic, or repurposing an existing drug, the selection of the right packaging is an essential step. The primary container, which is in direct contact with the drug product, plays a critical role in preserving the drug’s integrity from the initial point of production, packaging, distribution, and storage to the moment it is administered. The reliability of the primary container is also essential in ensuring safety for the patient or the healthcare practitioner, which, aside from the human impact, can have significant financial implications for the drug manufacturer if anything does go wrong.
Primary injectable drug packaging is usually composed of two parts: a glass container and a closure component. The latter must ensure the impermeable closure of the container and allow for an easy and safe collection of the drug product. Elastomers are the material of choice for these applications, but they also come with their own set of challenges in terms of integrity and safety. Compared with glass, which is mostly inert, rubber elastomers are the product of petrochemistry, requiring the use of various chemicals for vulcanization, and may therefore threaten the chemical integrity and safety of injectable drugs.
Except in specific cases, such as pre-filled syringes needle shields, and tip caps for which permeable rubbers are used (i.e., polyisoprene, styrene-butadiene), the pharma industry relies mostly on Halobutyls for its water/gas impermeability and especially the low level of chemicals they release, referred to as extractables and leachables (E&L). Over the years, the research and development activities of pharma rubber manufacturers have focused on optimizing Chlorobutyl and Bromobutyl formulations to limit the incidence of E&L while preserving the functional performances of the rubber.
In recent years, the pharma market has seen a significant rise in biologics. These highly complex molecules account for more than 70% of the current pharma market’s value, grew at an annual rate of 11% between 2018 and 2020 and are forecasted to grow globally at an annual rate of 9% through 2026.1,2 Over the past 5 years, four of the top five selling drugs in the US were injectable biologics, and 57% of the pharma pipeline consists of biologics.1,3 However, if biologics hold great promise for addressing unmet therapeutic needs, they are also highly sensitive, and choosing the right packaging is critical for successful drug development and delivery. In the context of COVID19, where the timely development of a vaccine is crucial, solutions that further minimize the risk of drug/container interaction are essential to ease regulatory approval and accelerate time-to-market.
These concerns can be addressed with coating technologies, which have demonstrated their ability to enhance drug-container compatibility. Ethylene tetrafluoroethylene (ETFE) films are the most common coating technology on the market. In principle, they form a physico-chemical barrier between the elastomer and the drug, helping to prevent the transfer of rubber chemicals into the solution. However, because of the repellant properties of the film and its relative stiffness, it cannot simply be applied all over the elastomer as it would likely tear and would prevent the elastomer from making direct contact with the glass to ensure container closure integrity.
To address these challenges, Aptar Pharma has developed PremiumCoat®, a line of vial stoppers and syringe plungers that combine the benefits of ETFE films with the quality of Aptar Pharma’s Bromobutyl formulation, proprietary designs, and state-of-the-art processes. The chemical performances of PremiumCoat® are demonstrated through a case study that compared the results of coated components with the results obtained with equivalent uncoated Bromobutyl components. The case study shows that the addition of the ETFE film greatly reduces the number and quantity of compounds that can be leached from the Bromobutyl, demonstrating that the ETFE film acts as a barrier that limits the transfer of E&L into the drug product.
SIMULATION STUDY, A TOOL FOR ASSESSING THE EFFICIENCY OF THE ETFE FILM
The choice of the closure component is crucial, and chemical performance is key to ensure patient safety. To illustrate this point, the early 2000s witnessed pure red blood cell aplasia (PRCA) cases spike after the use of Erythropoietin (EPO). Extractables from the rubber have been identified as a cause of EPO aggregates formation that may have in turn elicited an auto-immune response and caused PRCA.4,5
Extractables
The FDA defines extractables as all the organic and inorganic chemical species that can be released from the surfaces of components used in the manufacture and storage of drug products under laboratory conditions. Standard extractable studies are performed by fully submerging the elastomeric component in a solvent (water at different pH, with a range of organic solvents at varying polarities) and forcing the extraction by heating the system (Figure 1B). The extraction solution is then analyzed to identify and quantify the compounds that got extracted. This approach simulates extreme conditions and aims to identify all compounds that may be found in the final drug product. These studies are mandatory for regulatory submission, can be performed by the component supplier or the pharma company, and can help drug developers to better anticipate potential incompatibilities they may face during leachable studies.
Leachables
Leachables are defined as the organic and inorganic chemical species that can be released from the surfaces of components used in the manufacture and storage of drug products under conditions of normal use. Leachable studies, which represent real-life conditions, expose the elastomeric components to the actual drug solution (Figure 1C, which is then analyzed to identify compounds that have been leached from the rubber. These studies are often performed simultaneously with drug stability assays, as requested by regulatory bodies, and inform drug developers of the compounds that may be found in the drug product prior to patient administration.
Studies
In the case of film-coated elastomers, the film protects the part of the component that is exposed to the drug solution. Extractable studies do not evaluate the action of the film itself, as this requires the whole component to be immersed in the solution, including the non-coated parts. In order to quantify the benefits associated with the use of film-coated stoppers, Aptar Pharma’s experts have designed a bespoke simulation experiments.
In these experiments, the stopper is inserted onto the vial and inverted, so that only the relevant coated surface of the elastomer contacts the solution (Figure 1B). As opposed to leachable studies, which are specific to a drug and only relevant to a given situation, simulation studies focus on the volatile compounds (vial filled with air), semi-volatile, non-volatile, and ionic compounds (all vials were filled with solvent and inverted). Aptar Pharma’s specialists use a range of analytical methods to identify and quantify semi-volatile (gas chromatography-mass spectrometry), volatile compounds (headspace gas chromatography-Mass spectrometry), non-volatile compounds (Liquid chromatography-UV spectroscopy-Mass spectrometry), or ionic compounds (ion chromatography).
THE ETFE FILM ACTS AS A BARRIER THAT LIMITS EXTRACTABLES & LEACHABLES
Aptar Pharma’s expertise in injectables is based on years of research on rubber, which led to the development of dozens of proprietary formulations of polyisoprene, styrene butadiene, Chlorobutyl, and Bromobutyl. To address the most sensitive pharma markets, such as vaccines or biologics, Aptar Pharma released a state-of-the-art 6720GC grey Bromobutyl, and ships over 1 billion components to the pharma industry annually.
Aptar Pharma has pushed the chemical performances of its closure solutions even further by developing PremiumCoat®, a platform of products that combines the 6720GC formulation with a market proven ETFE film barrier. Aptar Pharma and Next Breath* experts have performed simulation studies to compare the chemical performance of PremiumCoat® with the equivalent uncoated Bromobutyl stopper, specifically assessing the efficiency of the ETFE film itself.
Figure 2 shows the simulated profile obtained by gas chromatography of a model solvent (water/ethanol 50/50) when exposed for 6 and 12 months to a PremiumCoat® or equivalent uncoated rubber component. On these chromatograms, each peak represents a specific chemical compound that has been leached from the rubber in these model situations, to the exception of the peak corresponding to the internal standard.
Overall, the PremiumCoat® chromatogram displays fewer peaks, with a lesser magnitude than the uncoated rubber. More specifically, in the first boxed region (between 9-11 minutes of retention time) PremiumCoat® displays a 76% (at 12 months) and 80% (at 24 months) reduction in leached compounds compared to the uncoated rubber. In the second boxed region (between 13-15 minutes of retention time), a reduction of 92% (at 12 months) and 93% (at 24 months) was observed. Finally, when looking at the majority peak in the uncoated rubber profile, we observe a 97% (12 at months) and 98% (at 24 months) reduction in quantity for this specific leached compound. The latter was identified to be a Fatty Acid Methyl Ester (FAME), a by-product of the vulcanization produced through the transesterification of fatty acids, which was not reported as a toxic agent for patients.
It is particularly important to note that when performing the simulation study on PremiumCoat®, no new peak was detected as compared to the uncoated rubber. This is a clear indication that the addition of new chemical elements in the film itself did not lead to new leachables in the profile.
These results demonstrably show the addition of the ETFE film on the surface of the Bromobutyl rubber reduced the number and quantity of compounds leached during this simulation study by up to 97%. This demonstrates the ETFE film acts as a barrier that significantly reduces the transfer of extractables and leachables into the drug solution. Similar results led to the same conclusions when performing the same simulation experiment with gamma-sterilized components (data not shown, available in the PremiumCoat® Data Packages).
PREMIUMCOAT®: PROTECTING YOUR DRUG & YOUR PATIENTS
In this study, we reviewed the information provided by extractables, leachables, and simulation studies:
- Extractable studies are designed to provide a complete picture of all the compounds that may be transferred into the drug product. They can be performed separately from the drug development process, but because the extraction conditions are harsh, they give a poor representation of what the final use situation is.
- Conversely, leachable studies accurately represent the final use situation and confirm that the drug and closure components are compatible. They can only be performed once the final drug formulation is defined, at the later stages of the development process.
- Simulation studies aim to inform drug developers of which compounds may actually be leached in different model situations, allowing them to anticipate much earlier in the process as to whether the closure component will be compatible with the final drug formulation.
Simulation studies are an invaluable tool for drug manufacturers who want to expedite their development process, allowing them to make informed decisions much earlier in the project, hence de-risking the choice of rubber closure component. The simulation studies performed with PremiumCoat® demonstrate the ETFE film greatly limits the number and quantity of extractables and leachables, making it a safe choice for sensitive drug developments.
Aptar Pharma has collaborated with Next Breath and other specialized service providers to produce Data Packages that provide customers with valuable information to help them choose PremiumCoat® with confidence, while accelerating the development process and regulatory approval. These Data Packages include complete simulation studies with various model solvents, glass container compatibility data, container closure integrity testing, as well as a full extractable file that can be used for regulatory submission.
Leveraging the expertise that resides within Aptar Pharma and its service companies (Next Breath, Gateway Analytical) allows for complete and bespoke Service Packages to customers. These tailor-made packages let you choose the level of support you need in performing complete primary container testing and/or full leachable studies, so that you can focus on your formulation and smoothen your development process with PremiumCoat®.
Using simulation studies, Aptar Pharma demonstrated PremiumCoat® chemical performances. When combined with pure Bromobutyl formulation, the ETFE film-coating technology forms a barrier that reduces the quantity of leachables transferred into the solution by up to 98%. PremiumCoat® can significantly reduce the risk inherent to E&L. Choosing PremiumCoat® with Data Packages and Service Packages will accelerate your drug development process and provide the best protection for your drug and your patients.
*Next Breath is a specialty company of Aptar Pharma, and a full-service cGMP compliant laboratory specializing in analytical testing of a range of drug delivery systems from early stage to commercialization.
REFERENCES
- Biologics market analysis internal studies. Aptar Pharma, 2021 (from IQVia 2021 extraction).
- Biologics market – Growth, Trends, Covid19 impact and forecast (2021-2026). Mordor Intelligence, 2021. https://www.mordorintelligence.com/industry-reports/biologics-market.
- “Medicine Spending and Affordability in the United States: Understanding Patients’ Costs for Medicines”. IQVIA Institute for Human Data Science, 2020. https://www.iqvia.com/insights/the-iqvia-institute/reports/medicine-spending-and-affordability-in-the-us.
- Richter C, Lipperheide C, Lipke U, Lamprecht A. Impact of extractables from rubber closures on protein stability under heat stress. Eur J Pharm Biopharm. 2018 Sep;130:22-29. doi: 10.1016/j.ejpb.2018.06.009. Epub 2018 Jun 9. PMID: 29894815.
- Sharma B. Immunogenicity of therapeutic proteins. Part 2: impact of container closures. Biotechnol Adv. 2007 May-Jun;25(3):318-24. doi: 10.1016/j.biotechadv.2007.01.006. Epub 2007 Jan 30. PMID: 17337336.
- Data source: NextBreath Simulation Study, [SR-2020-65], 2020, Baltimore MD, US.
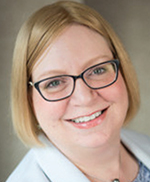
Dr. Julie D. Suman is the President of Next Breath, an Aptar Pharma company, and Manager of Scientific Affairs for Aptar Pharma. She earned her BSc in Pharmacy and her PhD in Pharmaceutical Sciences. She is co-editor for Respiratory Drug Delivery (RDD) Proceedings, and an Affiliate Assistant Professor in the Department of Pharmaceutics, Virginia Commonwealth University, VA. A Past-Chair of the AAPS Inhalation Technology Focus Group, Dr. Suman has published in several peer-reviewed journals and presented at numerous international meetings.
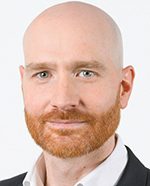
Sébastien Cordier is the Technical Product Manager for PremiumCoat® projects at Aptar Pharma’s Injectables division. A graduate of MINES ParisTech and EDHEC Business School in France, he first spent over 15 years in the automotive industry, where he developed a strong expertise in plastics and elastomers, before joining Aptar Pharma in 2020. In his current role as Technical Product Manager at Aptar Pharma, he is responsible for the PremiumCoat® platform of vial stoppers and syringe plungers, and is dedicated to supporting customer development projects involving coated elastomeric solutions.
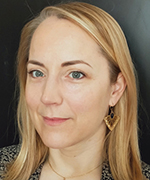
Estelle Verger is the Business Development Senior Manager for PremiumCoat® coated solutions for Aptar Pharma’s Injectables division and is responsible for the growth of the PremiumCoat® platform in the global injectable market. A graduate from ESSEC Business School and Fachhochschule Dortmund, with a Masters degree in International Business Management, she joined Aptar Pharma in 2011 as a Sales Manager, Injectables. She then moved to Aptar Pharma’s Consumer Healthcare division as a Product Manager, where she was responsible for Airless Dispensing Solutions for pharmaceutical applications for a number of years, before returning to the Aptar Pharma Injectables division in 2020.
Total Page Views: 5402