TUB PACKAGING - Why Double-Bagged Tubs Are an Issue for High-Speed Filling
INTRODUCTION
Fully automated production is fast becoming the standard for the biopharmaceutical manufacturing industry. At the same time, many fill and finish businesses are still struggling with a consistent source of variability in their automated production processes: inconsistently double-bagged tubs of pre-sterilized syringes.
Variation in tub packaging continues to create financial and operational challenges for the entire downstream supply chain. It’s time for our industry to align on packaging configuration requirements that make tubs fully processable on automated lines.
INCREASING DEMAND FOR PRE-STERILIZED FORMATS & QUALITY REQUIREMENTS
When pre-sterilized systems were introduced in the early 1980s, they were intended primarily for labs and small filling. They were packaged in a bag that simply had to keep its contents clean and sterile until it was opened. Unbagging a tub of syringes was a manual process with little impact on the small-scale use cases of the time.
But much has changed in 40 years. Today, pre-sterilized syringes are the requested industry standard for filling of prefilled syringes, which now make up a significant portion of the pharmaceutical injectables business. With the growing demand for these products, the aseptic production processes as well as quality and regulatory requirements have also changed. Pharmaceutical fill finish companies now increasingly rely on high-speed syringe-filling machines. This machinery can have a nominal output of >50,000 units per hour, or about six tubs of syringes every minute.
Production volumes this large have only been made possible by automating as many production steps as possible, including the process of unbagging tubs. Like any mechanized manufacturing system, today’s advanced filling lines depend on reproducible characteristics and precision, in both the filling steps they perform and the components they process. Variability of any kind can create significant challenges – and double-bagged nested syringes are one of the troublesome culprits.
Aseptic quality requirements are tightening, especially with new Annex 1 contamination regulations on the way. Double-bagging syringe tubs is a valuable sterility solution for these businesses, especially for those who aren’t using E-Beam sterilization equipment to sanitize the outside of the bag before a tub is introduced to a higher-level cleanroom. For drug manufacturers who don’t rely on this equipment, double-bagged tubs help enable compliance with aseptic quality requirements. As tubs move along the filling process, one bag can be removed each time the tub enters a higher cleanroom level.
THE DOUBLE BAGGING PROCESS: SOURCE OF VARIABILITY
The production challenges begin well upstream from the automated production lines, starting with the way primary containers are packaged by their manufacturers.
Nested, ready-to-use syringes are typically packaged in tubs that are sealed with a gas permeable foil and then bagged. Downstream production challenges often originate with the bagging process, which is still a manual one for most syringe suppliers. The process usually involves the following several steps:
- An operator places the tub in an inner bag, which is then sealed
- Since the inner bag is typically the same size as the outer bag, the sealed flaps of the inner bag are then folded up and fixed in position while the operator inserts the tub into the outer bag
- The outer bag is then also sealed for delivery
Unfortunately, this manual approach inevitably leaves these processes susceptible to inconsistency in the bagging results.
This lack of packaging standardization can be challenging for automated processing facilities, which depend on the repeat precision of every input to deliver the rigorous efficiency and distinctive quality that our industry now expects. For drug manufacturers who use mass volumes of pre-sterilized syringes, the biggest problem often begins when the outer bag is opened – the moment when challenges unfold along with the inconsistently packaged inner bag.
THE AUTOMATED UNBAGGING PROCESS AT THE FILLING SITE
In theory, this ought to be a straightforward process. Here’s how it’s typically designed to work:
- First, the outer bag is cut open and transferred.
- The tub with the remaining inner bag is pushed through an opening (“mouse hole”) into the cleanroom area.
- At this point, the folded inner bag should relax and unfurl before the tub reaches the cutting station at the mouse hole entry to the Class A cleanroom area. While most inner bags partially unfold due to restoring forces, process aids like mechanical guides and compressed air nozzles can help further unfold the bag to a flat flap that can be readily opened by a cutting device.
In reality, the results are often far less satisfactory. So where do the issues arise? In a nutshell, it is the incompatibility between the alignment of manual and automated process.
MANUAL BAGGING: A CHALLENGE FOR AUTOMATION
Most suppliers for primary packaging container continue to manually bag their tubs according to their own internal packaging specifications. This approach relies heavily on operating instructions and the frequency and quality of operator training to enable consistent outputs. The predictable result: considerable variability in the tub packaging, especially in the position and folding of the inner bag.
These variances create an impossible challenge for automated bag-opening machinery. No combination of relaxing forces and assistive equipment can resolve this level of variability to the point that every inner bag is fully compatible with the cutting step.
This challenge is then further compounded by three key factors: the way the inner bag flaps are folded, the position of the tub in the inner bag, and the inner bag material. Let’s take a closer look at how each one can impact an automated production line.
FOLDING PATTERN INNER BAG FLAPS
This challenge is most acutely clear when tubs arrive at the cutting station that will open the inner bag and release the tub through the filling room mouse hole. At this critical process step, partially or inconsistently unfolded inner bags create a cascade of disruptively variable cutting results.
Some bags will be cut partly open and then get stuck when high resistance forces prohibit the forwarding mechanism from advancing the tub. Sometimes the cutting tools strike misaligned inner bag folds at an angle to the axis of the tub, resulting in torsional force that twists the bag and tub and stops the processing machinery. At this process step, manual intervention to open the inner bag is not possible, as the inside and content of the bag must remain sterile to enable contamination-free presentation to the Class A area. Instead, the partially opened tubs must be removed by hand and discarded.
POSITION OF THE TUB IN THE INNER BAG
Furthermore, not all tubs approaching the cutting station are properly positioned in their inner bags, which can also affect the consistency of the rectangular bag cut resulting in machine stoppages and manual intervention.
This begs a natural question: had the bagged tubs been decentered during earlier processing steps, or had the tubs been misaligned during manual packaging? Tracing tubs back to the input station quickly demonstrates that the latter is usually the case. When tubs arrive at the drug manufacturer, many of them have being found not centered relative to the inner bag or inserted as far into the bag as possible, the correct position for automated unbagging.
Unfortunately, these inconsistencies in the folding pattern of the inner bag flaps and the position of the tub in the bag are both difficult for an operator at the filling site to assess from the outside of the bag. Auditing and presorting tubs based on bag alignment is neither practical nor feasible at the filling machine entry, when the operator is focused on loading the conveyor belt and has no control over the alignment of the tub inside its bag. At this point, not even optimal operator instruction or training will compensate for misaligned tubs or inconsistent bag folding. Ultimately, the quality of the output depends on the consistency of the input.
THE INFLUENCE OF THE INNER BAG MATERIAL
Different qualities of the inner bag material can strongly impact the way bagged tubs behave in the manufacturing area, as well as in the subsequent unbagging process in the filling site. The material compound, foil thickness, and the stiffness of the plastic foil can all influence the way relaxing forces take effect on the unfolding bag flaps. The material’s surface friction properties and adhesiveness can also vary significantly. These machinability variables can not only require adjustments in standard processing parameters, but also demand hardware modifications when bag material properties differ widely enough.
Variable bag characteristics can be especially challenging for mechanical guides or travers feeding devices designed help unfold inner bags or direct them with a controlled movement (like on a cutting station). Outlet belts for cut-off bag sections can also be critically impacted: if these sections are too stiff or tacky, they may not readily bend or slip through channels or tubes on their way to a disposal box. Because the machine parts associated with these steps are typically integrated into the machine bed, they are not as readily replaceable as format parts. Consequently, bag characteristics that require hardware modifications are often a reason for declaring syringe tubs “non-processable.”
In our experience, automated unbagging processes are consistently successful for some bag materials, but far less so for others. The cost and efficiency implications are all too clear. Not surprisingly, the question comes up whether it’s reasonable to expect pharmaceutical filling lines to absorb the impact of this lack of standardization.
ECONOMIC IMPACT
Folding pattern of inner bags, positioning in the inner bag, inner bag material: all these variables can contribute to a significant number of production interruptions.
An inner bag that cannot be properly cut stops the machine. Because manually opening the bag will break sterility protocol, the tub must be removed by hand and then discarded. One hundred and sixty syringes are lost. At that point, the machinery will have experienced about 40 seconds of downtime. During this time, another four tubs could have been processed. The fill and finish business loses not just the value of the syringes and production time, but also sees a severe impact on machine utilization and overall equipment efficiency (OEE).
And what is the economic cost involved? Consider the progressive ratio of lost high-value syringes for biotech applications, to lost production time, to unplanned extension of batch manufacturing times. Calculating this model, a 10% rate of non-processable tubs caused by inconsistently folded bags correlates with a roughly 50% increase in batch production time – with a corresponding and significant impact on production costs and customer satisfaction.
STEPS TOWARD SOLVING THESE CHALLENGES
Fortunately for our industry, the issues created by inconsistent bagging processes are readily addressable with the right approach. The position of the tub is particularly important. Figure 3 shows a schematic drawing with important criteria:
- The tub is inserted all the way to the end of the bag
- The tub is centered in the bag
- Bags have a printed indicator of the correct tub position to help operators achieve consistent results
- Air is expelled from the inner bag in order to avoid “loose” tubs that can change position during the unbagging process consistently
- Bag weld is consistently flat
- The bag material is specified always the same to enable consistency
And finally, the folding method for the inner bag flaps is specified and uniform to enable that the inner bags can be fully and consistently unfolded before they reach the cutting station.
Today, none of these steps are subject to specification or standardization. From our point of view, this must be changed.
AUTOMATED BAGGING PROCESS & STANDARDIZATION
The efficiency and productivity of pharmaceutical producers is handicapped by “plastic bags.” Fortunately, there’s a solution to this challenge: automated bagging equipment. This investment can lead to the consistent, reproducible bag configurations that the drug manufacturer relies on, without the variable folding and unpredictable configurations of manual bagging processes. But again: Which folding scheme (according to Figure 1) is this machine equipment is designed for?
The 2015 ISO 11040-7, Packaging Systems for Sterilized Sub-Assembled Syringes Ready for Filling, agreed among other things on measures for tubs, nests, and bags. However, to support fully automated handling of double-bagged tubs, all the specifications described here – inner flap folding schemes, the tub position in the bag, smaller tolerances of the bag dimensions – are preferable to incorporated into the next revision of the ISO. These changes can help our whole industry drive down inefficiency and waste in the processing of pre-sterilized syringes.
Today, double-bagging processes have some distance to go to reach this valuable goal. We hope to soon see some progress toward the same level of standardization that our industry continues to aspire to and achieve.
To view this issue and all back issues online, please visit www.drug-dev.com.
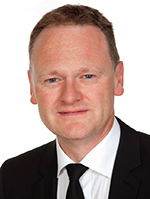
Tilman Roedle is Lead Expert Drug Delivery Systems for Vetter. He deals intensively with strategic industry collaborations on innovative drug delivery systems and Quality Management for medical device development. He joined Vetter in 2003 as Project Manager, Packaging Development and was appointed Director of Packaging Development in 2005. In this position, he was responsible for primary packaging materials for parenterals and drug delivery systems, later including secondary packaging as well as automated visual inspection implementation and process qualification to help ensure cGMP. His career began in 1996 as a Design Engineer in special machinery for the automotive industry, and later worked as a Project Manager for special machinery investment projects. He earned his Master’s degree in Mechanical Engineering at the University of Stuttgart, Germany, in 1995, focusing his studies on key aspects of design and materials sciences.
Total Page Views: 7055