Issue:October 2021
SYRINGE PLUNGER - Exploring How the Functional Properties of the PremiumCoat® 1-3-mL Plunger Facilitate its Implementation on Filling Lines & Enable the Delivery of Sensitive Vaccines & Biotech Drugs
INTRODUCTION
Whether in the development of new drug products, managing a molecule’s life cycle, or when repurposing existing drugs, the choice of primary packaging is of utmost importance. It is essential that drug manufacturers understand the properties of their packaging to ensure the success of their project. The primary container, because it is in direct contact with the drug product, plays a central role in ensuring the drug is protected over time, from filling through to short- or long-term storage, and to the point of administration to the patient. Primary container failure may compromise the drug’s integrity, which, aside from financial implications for the drug manufacturer, can seriously put patients at risk.
To fight Covid-19, the industry developed highly-sensitive vaccine technologies and turned to coated elastomeric closure components to minimize development risk, which put an unusual strain on global availability and led to a significant increase in lead-time for these components. As the fight against the global pandemic persists and vaccination campaigns continue to be rolled-out, the emergence of new Covid-19 variants suggests that, once under control, this pandemic could become a seasonal epidemic. Drawing from our experience with the flu, we know seasonal vaccination is very different from the mass-vaccination context we are currently experiencing. Instead of relying on large vaccination centers, where many vaccinations are performed sequentially, seasonal vaccines are usually administered by trained nurses, physicians, or even pharmacists, directly from their respective healthcare settings. In this context, single-dose Pre-Filled Syringes (PFS) become highly relevant, as they limit drug waste compared to multi-dose vials, and significantly simplify the administration process. Furthermore, pharma companies and contract manufacturing organizations are looking to strengthen their supply chains to ensure they can sustain spikes in demand or avoid exclusive dependency on suppliers. As such, the validation of a second source of supply is an ideal strategy to de-risk operations and ensure long-term security of supply.
Aptar Pharma has leveraged 50 years of expertise in the development and manufacturing of PFS components to further add to the PremiumCoat® platform with the introduction of the 1-3mL syringe plunger format. Building on the success of PremiumCoat 1mL long film-coated stopper’s technology and partnership with BD, the PremiumCoat 1-3mL syringe plunger combines a pure Bromobutyl formulation with a market-proven Ethylene tetrafluoroethylene (ETFE) film that acts as a barrier to limit the transfer of rubber leachables into the drug product. The 1-3mL plunger addresses the needs of sensitive vaccines, large-volume biologics, and facilitates vial-to-prefill projects. Aptar Pharma performed a series of tests to demonstrate how the PremiumCoat 1-3mL syringe plunger operates on different filling lines and how its properties may facilitate manual injection and auto-injector integration, while preserving the drug’s integrity.
PREMIUMCOAT® 1-3ML CAN BE HANDLED BY BOTH VENTED & VACUUM STOPPERING MACHINES
Once the drug is filled in the PFS, the plunger is inserted to seal the device via one of the two main methods frequently used on the market. The first is referred to as vented placement and relies on the insertion of a hollow tube inside the PFS called the vent tube. The plunger is placed on an insertion rod, forced through the vent tube, and exits on the other side to expand into the PFS, with the air being vented out around the stopper to avoid pressure building up. Though this method is preferred on high-speed filling lines for its rapidity and relatively easy implementation, it generates a bubble in the syringe, which may lead to further issues, for example, when transporting the filled syringe in a depressed environment such as a cargo plane. Furthermore, because the plunger is forced through a tube with a smaller diameter than that of the syringe, it induces a significant deformation of the elastomer. This may be particularly critical in the case of film-coated plungers and may impair the film’s integrity, as observed with other ETFE-coated stoppers, which may negatively affect the drug-plunger compatibility.1
The second plunger placement method is the vacuum placement. It relies on the creation of a vacuum in the filling environment and positioning of the plunger at the top of the syringe. Upon restoration of atmospheric pressure, the differential pressure pulls the plunger inside the syringe barrel. This method significantly limits the size of the bubble and does not deform the plunger, thus preserving the integrity of the film coating. However, this method is usually slower than vented placement.
Aptar Pharma’s PremiumCoat 1-3mL ETFE film-coated plunger was tested with both vacuum and vent-tube stoppering machines from various manufacturers. With the latter, the integrity of the ETFE film was controlled by camera inspection before and after insertion.
PremiumCoat 1-3mL was found to perform well in the bowls and rails. The plungers did not stick to each other and were efficiently oriented before being fed into the rails, through which the plungers travelled easily. Testing of the vacuum and vented placements showed consistently good placement of the ribs, which were well positioned, and the film was found to be unaltered (Figure 1A). In the case of vented insertion, which is known for altering ETFE-films in other coated plungers, the surface electron micrographs show that, regardless of the vent-tube diameter, the film remains intact after insertion (Figure 1B).
These data confirm that, at this stage of development, PremiumCoat 1-3mL plungers are compatible with both vacuum and vent-tube technologies, facilitating the implementation of PremiumCoat on customer filling lines. The demonstrated compatibility with vented placement unlocks new opportunities for vaccine manufacturers working with high-speed vent-tube filling lines who wish to secure their drug development with ETFE film-coated plungers.
PREMIUMCOAT® 1-3ML PLUNGERS MAINTAIN CONTAINER CLOSURE INTEGRITY DURING TRANSPORT
Syringes stoppered using the vented method can include a bubble that is in contact with the plunger. When PFS are then transported by plane, they may be xposed to a significant reduction in atmospheric pressure within cargo environments. Because of the pressure difference and the presence of a bubble, the plunger is likely to move outward. Even though PFS are packaged in aseptic conditions, only the inside of the PFS is guaranteed to be sterile, and a significant outward movement of the plunger may expose the drug to a section of the glass where sterility is not ensured.
To investigate this possibility, Aptar Pharma performed a test in which the syringes filled with a solution also included a bubble of defined size. The PFS were exposed to a depression of equivalent magnitude to a cargo flight, and the movement of the plunger was measured. The container sterility is considered compromised if a plunger moves more than twice the inter-rib distance. Because the plunger is composed of three ribs, a movement of two inter-rib would place the rib on the drug side at the position of the rib initially on the outside, therefore exposing it to the external environment.
While vacuum plunger placement minimizes the size of the headspace bubbles (typically below 1 mm), vented placement can generate bubbles of up to 6 mm in a worst-case scenario. Figure 2B shows that, even with a 6 mm headspace, the PremiumCoat 1-3mL plunger’s movement remains largely below the reject criteria, and the plunger moves by less than one inter-rib distance.
These results indicate that, under the conditions of these tests, the PremiumCoat 1-3mL plunger ensures the drug remains sterile during air freight, even if a sub-optimal vented placement was operated.
PREMIUMCOAT® 1-3ML PLUNGER FACILITATES INJECTIONS & AUTO-INJECTOR INTEGRATION
The break-loose force describes the strength required to initiate the movement of the plunger in the barrel, while the gliding force designates the strength needed to continue this movement. These parameters are essential to a successful injection, as they are directly related to the ease-of-use of a PFS and define whether the PFS could be integrated in an auto-injector to facilitate further improvement in the injection process.
When the plunger is inserted into the syringe barrel, it may be stored for a prolonged period, during which the rubber is in contact with the glass. Because the plunger must maintain container closure integrity, its diameter is designed to be slightly higher than that of the barrel to maintain a degree of compression and ensure container closure integrity. In order to facilitate the movement of the plunger inside the barrel, both the glass and the rubber are lubricated with silicon oil. The break-loose and gliding forces therefore depend directly on the siliconization process and the design of the plunger. These values help facilitate the manual injection process, with lower forces usually associated with a perceived ease of injection. On the other hand, variability of break-loose and gliding forces between products is essential in enabling auto-injector integration. These secondary devices use mechanical springs whose force is carefully controlled; a weak spring would not enable the delivery of the drug under an appropriate time, while a spring that is too strong may be associated with painful injections.
With the increased use of biologics, and ongoing efforts to improve adherence and comfort of injections in the context of chronic disease treatment, pharma manufacturers are looking to reduce the number of doses that patients need to receive via injection. This is typically done by increasing both the volume of the injection and the concentration of the drug, with the latter leading to an increase in the viscosity of the solution. Therefore, injection devices must ensure that the delivery of such solutions can be performed as expected, with or without an auto-injector. This again depends on the functional performance of the elastomeric plunger in conjunction with the syringe.
Aptar Pharma’s technical experts assessed the break-loose and gliding forces of PremiumCoat 1-3mL plungers when inserted into different syringe barrels and with fluids of various viscosities. These forces were measured using a dynamometer as the plunger travelled through the barrel at constant speed. Each measurement yields a graph of forces which is analysed to extract the break-loose force and average gliding forces.
When comparing syringes from two different suppliers, Aptar Pharma’s PremiumCoat demonstrated consistent break-loose and gliding performance (Figure 3A). For a given syringe, aging was observed to lead to a mild increase of the break-loose force (less than 3N) but no increase of the gliding force. In all cases, over the 15 replicates, the results show very little variability, indicating consistent performance across plungers.
When simulating an injection with solutions of various viscosity, we observed a gradual increase of both the break-loose and gliding force (Figure 3A). This increase was expected according to Poiseuille’s law, which states that the force in such a system is directly proportional to the viscosity of the fluid. It is interesting to note that the difference between the break-loose and gliding force remains similar for each condition. This indicates that the solution’s viscosity does not significantly affect the performance of the PremiumCoat plunger, and the forces remain under 25 N.
Taken together, these results demonstrate that the Aptar Pharma PremiumCoat 1-3mL plunger performs consistently well in biotech syringes, enabling the delivery of high-viscosity drugs. The low break-loose and gliding forces are compatible with manual injection, and remain within a patient’s abilities, even for those suffering from rheumatoid arthritis who can deliver average forces of at least 30 N.2 The low variability within the sample and high consistency between break-loose and gliding force indicate that PremiumCoat 1-3mL would facilitate integration into an auto-injector.
APTAR PHARMA’S PREMIUMCOAT® 1-3ML-PLUNGER FULFILLS KEY DRUG DELIVERY REQUIREMENTS FOR VACCINE & BIOTECH APPLICATIONS
At this stage of Aptar Pharma’s PremiumCoat 1-3mL plungers development, the series of validation testing performed on the product show promising results and demonstrate that the product meets key requirements for addressing sensitive vaccines and biotech drugs:
- PremiumCoat performed well on vacuum filling lines and, in contrast with other film-coated plungers, can be processed by vent-tube technology without altering the film’s integrity.1 Aptar Pharma’s plunger can therefore be easily integrated on common filling lines, including high-speed filling lines that use vented placement.
- When using air freight, and even in the case of a large headspace, PremiumCoat plunger movements remain controlled and do not jeopardize the drug’s integrity.
- PremiumCoat 1-3mL plungers perform well in glass syringes, and the force required to perform an injection remains largely within a patient’s capabilities. The consistency of the break-loose and gliding forces across situations and aging may facilitate the integration into auto-injectors.
REFERENCES
- Pharmaceutical Technology Editors. “Stoppering Techniques for Prefilled Syringes”, Equipment and processing reports (2008) https://www.pharmtech.com/view/stoppering-techniques-prefilled-syringes.
- Silva, Graziela Sferra da, Mariana de Almeida Lourenço, and Marcos Renato de Assis. “Hand strength in patients with RA correlates strongly with function but not with activity of disease.” Advances in Rheumatology 58 (2019).
To view this issue and all back issues online, please visit www.drug-dev.com.
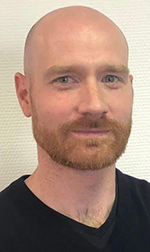
Sébastien Cordier is the Technical Product Manager for PremiumCoat® projects at Aptar Pharma’s Injectables division. A graduate of MINES ParisTech and EDHEC Business School in France, he spent over 15 years in the automotive industry, where he developed a strong expertise in plastics and elastomers, before joining Aptar Pharma in 2020. In his current role as Technical Product Manager at Aptar Pharma, he is responsible for the PremiumCoat platform of vial stoppers and syringe plungers, and is dedicated to supporting customer development projects involving coated elastomeric solutions.
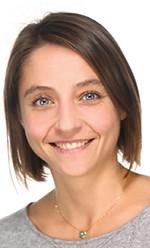
Dr. Laure-Hélène Guillemot is Project Leader within Aptar Pharma’s Injectables division. An engineering graduate of the Superior School of Chemistry Physics and Electronics, Lyon, France, she also earned her PhD in Chemical Physics from CEA-Leti, Grenoble, France. Having worked over 6 years in the construction products industry, she developed a strong expertise in glass chemistry and project management for product development. She joined Aptar Pharma in 2020 and in her current role is involved with new product development, including Aptar Pharma’s PremiumCoat® solutions.
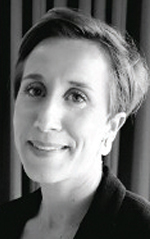
Audrey Chardonnet is the Global Business Development Director for Prefillable Syringe Components (PFS) at Aptar Pharma’s Injectables division and is responsible for driving overall strategy for PFS segments. She previously held several positions within the Aptar Pharma sales organization, most recently as Director, Global Strategic Customers, with a particular focus on business development with syringe manufacturers. She graduated with an Engineering Master’s Degree in Chemistry and has over 12 years of experience in the injectables industry.
Total Page Views: 9444