Issue:April 2022
SUPPLY CHAIN MANAGEMENT- Are Supply Chains Up for the Post-Pandemic Challenge?
INTRODUCTION
During the pandemic, medical technology businesses are likely to have identified stress points and vulnerabilities in supply chain infrastructures and operations that might otherwise have remained unnoticed. The struggles to address both peaks and troughs in product demand in a time of extreme uncertainty has helped bring weak links to light. These weak links, now that they have come to the forefront, must be tackled immediately in order to face any future pandemic waves or knock-on effects, and to prepare a solid front for any other unexpected events that may impact the market and supply chain.
Troubleshooting any weaknesses detected within the supply chain is key to preserving market dynamics from disruption to long supply chains, ensuring the immediate reprioritising of supplies critical for patient treatments, and preparing for the forthcoming flood of pent-up demand for postponed elective procedures. Failure in the medical device supply chain simply cannot be an option, as lack of stock may impact scheduling of future diagnosis and treatment, including drug administration, and ultimately put lives in danger. It is therefore urgent businesses update their policies to include plans for operational continuity, disaster prevention, and business recovery in order to minimize the impact of future disruptions on product supply.
In addition to this, assessing supply chain risks should not be an ad hoc activity but an iterative process that is carried out periodically and continuously with the objective of keeping risk as low as reasonably possible. In fact, supply chain models come with risks by definition: the just-in-time (JIT) model for instance, while it has advantages, such as reduced storage fees, a reduction in waste and therefore carbon emissions as well as greater flexibility in inventory management, has a very slim margin of error and typically requires a series of back-up plans to prevent any problems. Whatever the supply chain model, however, a risk assessment can only be beneficial, and it might be well overdue.
THE MANUFACTURING MACHINE
The risk assessment process should ideally start within manufacturing plants. Here, it is advisable to review engineering spares policies, equipment, and assets usage and check that service level agreements are in place covering both the appropriate depth and frequency of service. Clear schedules and governance guidelines must be put into place to make sure that manufacturing controls are working as expected, and each key process in the manufacture of medical devices must be reviewed in light of recent pandemic experiences. It is vital to determine whether processes are still fit for purpose, whether risk parameters have changed, or a change in conditions dictates the need for new risk mitigation strategies. After completing this analysis, businesses will need to make sure their response is agile and flexible enough to deal with peaks and troughs in product demand. This may require additional investments, for example, execution of moulding or assembly capabilities for medical devices across alternative or multiple sites.
APPRAISING SUPPLIER NETWORKS
Supply shortages (15%), lack of alternatives (12%), and delays in production issues (12%) are some of the top post-pandemic concerns identified in a recent survey of supply chain professionals in the medtech industry.1 One case in point is the polymer industry, which supplies medical device manufacturers; this sector has not yet recovered from the effects of the pandemic and as a result, downstream markets are experiencing longer lead times from suppliers and extended door-to-door shipping times for multiple routes and shipping lanes.2 Reasons for these delays may include a surge in plastic products demand, a global shortage of shipping containers, and interruptions in production schedules.3
The same survey suggests that to prepare for potential natural disasters or other unforeseeable circumstances, manufacturers should improve the qualifications of multiple suppliers and of the review process (14%), try to source locally (16%), improve the visibility of supplier inventory, capacity, and lead times (13%), and endorse the restructuring of supply chains with second sources (12%). The availability of raw materials in different parts of the world of course impacts the ability of businesses to source locally, but they must also remain well aware of the exposure that source countries have to natural disasters, political instability, and other events that might impact the supply chain.
Keeping up to date with news and developments relating to the supply chain is therefore another critical activity for manufacturers. To do so, they will need a rigorous and comprehensive tracking and a management process that ensures early notification on potential disruption to supply and a consequent quicker implementation of mitigation activities to avoid or minimise future impact.
A CHECKLIST FOR SUPPLY CHAIN REVIEW
Based on the latest assessment of their supply chain, businesses may need to take action to mitigate issues caused by further and not yet known vulnerabilities among suppliers. The following dozen points in the checklist cover typical areas to keep under close control:
- Manufacturing suppliers’ site changes, mergers, acquisitions, market volatility
- Regulatory compliance (current and future trends)
- Product lifecycle reduction, eg, obsolescence of raw materials
- Supplier constraints, such as capacity, capability, low volume challenges, and logistical risks
- Supplier solvency and financial health
- Risks due to supplier reliance on raw materials and concentration in countries likely to be impacted by climate change
- Supply chain disclosure aligned with appropriate policies, eg, regulatory, commitment to low carbon emissions
- Reliance on single-sourced key strategic items
- Supplier material/process changes and notification of change
- Uncertainty and level of understanding of the supply chain, role of distributors, upstream manufacturers, complex supplier networks, complete processes, and supplier maps
- Pre-screening and auditing of supplier quality
-Organisation quality process assets
-Manufacturing/processing equipment
-State-of art health check
-Potential internal process failures
SUPPLY CHAIN MAPPING
The results of the assessment should be used to draw up a supply chain map of the procurement path of tier one and sub-tier suppliers for key purchased and manufactured items. This type of graphical or tabular representation is ideal to ensure everyone in the business clearly understands the process and potential risks. It can prove a vital tool in today’s post-pandemic recovery but should be part of regular best practice as it will support regulatory activities, such as tracking Economic Operator compliance under the EU Medical Device Regulation (MDR), which makes Manufacturers, Importers, and Authorized Representatives jointly and severally liable for nonconformities.
Supply chain mapping is particularly useful in highlighting:
- Supplier names, sites, and geographical locations
- Single source relative supply chain risk score
- Dual-source alternatives and preferences for primary and secondary sourcing
- Material demand chain: material type, processes, distribution, sub-tier suppliers (first level)
- Strategic and generic procurement, supplier agreements, including robust, active Notification of Change processes and aligned safety stock policies
- Validation level information and recovery time objectives
- Commercial engagement splits for dual-sourced, fully validated supply chains
ASSESSING NEEDS FOR NEW PRODUCTS
Finally, manufacturers should closely reconsider new products that are being developed, as they are, by definition, dynamic, and require an alignment between operational, business, and product strategies. New products also require an evaluation of the production and distribution model that needs to be built taking into consideration initial launch requirements and future demand. This may vary depending on each product and on whether the launch protocols are for a bespoke device for individual customers (such as a customized auto-injector) or a platform design for multiple customers (such as a safety device for prefilled syringes); the latter is likely to have a low-volume introduction but a forecasted growth to high volume. Businesses therefore need to identify potential risks to ongoing product supply to support product growth and meet demand. A scale-up strategy is essential to make appropriate decisions relating to tool investment, tool cavitation, assembly investment, or transition from low-volume engineered fixtures to full automation.
PROACTIVE PLANNING
Each medical device manufacturer will discover different patterns of risk as a result of COVID-19. It is therefore imperative that businesses carry out an in-depth and urgent re-appraisal of their supply chain, as failing to do so may cause commercial damage. Some of the changes we are now experiencing may become permanent, and the pandemic has alerted businesses, governments, and regulators alike to risks in the medtech supply chain, which were previously under-recognized or even invisible. Setting up best practice systems and processes to ensure the supply chain is critically assessed regularly is not only an important practice to face the current challenges, but will stand a business in good stead for any future unexpected changes in the supply chain. Manufacturers that begin their appraisal sooner rather than later are more likely to be well prepared, capable of weathering future storms, and able to grasp competitive advantage.
REFERENCES
- Managed Healthcare Executive, Study Reveals Path to Recovery in the Global Medical Device Supply Chain, 11. November 2020.
- Williams SC, “Plastics Shortage Hits Plastic Parts Supply Chain”. ISM Blog, Apr 2021.
- Williams SC, “Plastics Shortage Hits Plastic Parts Supply Chain”. ISM Blog, Apr 2021.
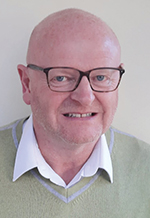
John Swift is Head of Supply Chain at Owen Mumford Ltd. He is an experienced operations program manager with a successful track record working throughout the supply chain, covering procurement, supplier management, invention, development and manufacture, as well as promotion, sales, and distribution. He is experienced in applying and adapting skills across both large corporations – such as Abbott, Abbvie, and Tyco – and SMEs, and has worked in multiple industries, including medical device, aerospace and defence, rail, chemical, automotive, and printing.
Total Page Views: 4011