Issue:May 2024
SCALING MANUFACTURING - Collaboration Between a Device Supplier & Equipment Manufacturer to Meet the Needs of Patients, End-Users & Pharma Manufacturers
INTRODUCTION
Emerging trends in the pharmaceutical industry are posing greater challenges to the successful delivery of injectables than ever before. This requires innovation in drug delivery systems to address these challenges and meet the needs of pharmaceutical manufacturers, the drugs they are developing, and the end-users and patients that deliver them and benefit from them. But delivering innovation in drug delivery is hard. Robust controls must be demonstrated to address the understandable aversion to risk. Pipeline drug programs continue or are terminated based on clinical data and evolving corporate strategies, requiring flexibility. New device programs are not fully funded until clinical success is probable, demanding speed to market once green-lighted. These factors require delivery systems that solve a wide array of challenges with a breadth of variants, and a manufacturing capability with the flexibility to produce them.
Credence MedSystems, an innovator of drug delivery systems, chose Mikron Automation, a leading partner for scalable and customized assembly solutions, to build an assembly system capable of producing over 150 variants of Credence’s Companion® and Dual Chamber™ (DCS) Syringe Systems. The Flexible Clinical Line will operate under cGMP controls to support combination product development activities, such as device verification and validation, stability studies, and clinical trials. The following discusses the industry trends driving challenges in drug delivery, how the Credence products produced on the Flexible Clinical Line address those challenges, and how the Mikron MiniCell automation platform was leveraged to allow the flexibility and speed-to-market required to support Pharma’s needs.
EMERGING TRENDS & THE RESULTING CHALLENGES
Healthcare in the home. Ongoing safety concerns. Sustainability’s emergence as a priority. New formulations and combined therapies. Heightened regulatory scrutiny. Cost and efficiency pressures. These and other trends in our industry are driving new or intensified challenges in the delivery of injectable medications.
Chronic diseases are being treated with medications administered by self-injectors and their loved ones. Hospital-At-Home legislation, implemented to address pandemic-driven healthcare capacity constraints, is continuing to allow acute care to be delivered in the home under hospital-based requirements. As healthcare continues to move to the home, these injections are being performed by less experienced end-users with limited training and support. Concurrently, formulations are becoming more complex. With pharma extending dosing schedules, higher concentrations with higher viscosities are being injected in higher dose volumes. The difficulty of achieving liquid-stable solutions persists and pharma is moving toward combining multiple therapies in such areas as xRNA therapies, vaccines, and GLP-1s. This is driving increased development timelines and expense to target stable formulations or co-formulations, or alternatively, is causing pharma to compromise by launching therapies in inadequate configurations that burden users and pose safety and efficacy risks during administration. Further, accidental needlestick injuries and syringe reuse continue to pose safety challenges. In short, drugs that are more difficult to administer are being administered by less-experienced users while requirements for safety, accurate dosing, and adherence are intensifying.
Additionally, the increased attention to sustainability, which seems to have finally arrived as an industry imperative, means that solutions to these challenges must come with reduced waste. And with intensified scrutiny on the performance of injection systems, devices must perform to heightened levels to drive complaints down. All of this must be achieved under the specter of ongoing pressures for cost and expense containment.
SOLUTIONS TO THESE CHALLENGES VIA INNOVATION
New trends create new challenges, and new challenges require innovative solutions. First considering the patient and end-user, a preferred delivery system can promote proper use and support adherence, which is linked to improved outcomes. Antalfy et al cite a series of studies showing that poor medication adherence worsens outcomes.1 The Credence Companion, which has numerous usability advantages designed to promote adherence, has been demonstrated as preferred by self-injectors as well as HCP’s.2 Key preferred elements include the ease-of-use, ease-of-safety activation, and the end-of-dose cues in the form of a tactile and audible click at the end of injection when the needle automatically retracts into the plunger rod. The melding of user cues, passive integrated safety, and reuse prevention can promote adherence while addressing the continuing safety and economic risks associated with accidental needlestick and syringe reuse.
While the Dual Chamber Syringe (DCS) includes the same usability and safety advantages seen in Companion, it further incorporates simplified administration of drugs requiring separation of constituents during storage due to stability or co-formulation challenges. The DCS platform includes two variants; the Reconstitution DCS allows transfer of the diluent from the rear chamber into the front chamber to mix with the lyo cake, powder, or liquid before injection, while the Sequential DCS allows injection of two liquids in sequence. This simplified usability is vital to enabling delivery of medication in the home, where users ranging from naïve self-injectors to HCPs will administer the medication. Further, the prefilled nature of the DCS and the elimination of numerous user steps reduce the risk of mis-dosing and the wasted dead volume (estimated at 20%-30%) associated with conventional vial kits. Risk of contamination and time to administer are also reduced (Figure 1).
It is relatively straightforward to connect enhanced usability with adherence, or to see how enhanced safety protects users and improves the overall cost of healthcare by reducing downstream expense resulting from accidental needlestick or syringe reuse. Less obvious, perhaps, is that solving usability and adherence challenges can lead to significant savings in development time and expense for drugs requiring separation during storage. As the usability and dose accuracy of dual chamber systems approach those of conventional single-chamber prefilled syringe presentations, new drug candidates can be introduced to the market faster because users can successfully use them. Reduced speed to market means the potential for market leadership and increased revenue, as well as significantly lower development cost that were traditionally directed at achieving stable formulations.
As the industry addresses the economic challenges associated with drug delivery, both sustainability and cost of ownership should be discussed together. With elderly population growth and increased prevalence of chronic disease, along with the vast amounts of disposables consumed by our industry, sustainability for sustainability’s sake should be enough to make it an imperative. But too often, sustainability and cost savings are presented as mutually exclusive propositions. When innovation allows sustainability advantages to be a driver of cost savings, rather than of increased cost, sustainability becomes an imperative that is much more implementable.
The Credence Companion, with its integrated safety mechanism, has been evaluated against the conventional safety device, an add-on that wraps around the syringe barrel.3 In that study comparing the 1-mL Long format, Companion was shown to reduce the weight of added components by 54%, utilize 40% of the plastic, occupy 47% of the volume pre-use, and occupy 33% of the volume post-use (Figure 2).
Each of these has obvious connections to an improved sustainability profile and has direct connections to cost savings. Large pharma manufacturers are paying for credits to offset their plastic waste. In addition to the cost, some experts believe this approach is less effective in reducing plastic pollution, and the only way to do so is to reduce plastic consumption, which Companion does.4 Reducing weight translates to reduced cost of shipping throughout the supply chain. Smaller footprint means smaller secondary packaging, which translates to lower cost of materials, further reduced waste, and more effective use of shelf space – the latter being especially impactful in drugs requiring cold-chain storage. These significant improvements will be notably enhanced in a 2.25-ml format in which the larger add-on device drives even more plastic, weight, and footprint while Companion has minimal change.
Companion’s cost-of-ownership advantages extend beyond those linked directly to sustainability. The conventional add-on device requires dedicated equipment to mount the safety mechanism on an already-filled syringe. That capital expenditure is not needed with Companion. Additionally, ongoing operational savings also result from the following:
- Any build-up of scrap associated with the add-on assembly machine includes an already filled syringe. The disposal or rework of that scrap, which includes the drug product, is costly. This expense is eliminated with Companion.
- For every pallet of syringes that will be paired with an add-on device, there will be an additional pallet of add-on devices. The expenses associated with the storage and material transport of the additional pallets are eliminated.
- When the add-on safety mechanism prematurely activates during transit or preparation, the medication cannot be injected, which is the ultimate failure of a drug delivery device. The cost of these complaints and associated customer dissatisfaction is eliminated with Companion because its mechanism of action dictates the needle cannot retract until the plunger rod has reached the bottom of the barrel.
INNOVATION EXTENDS BEYOND PRODUCT & INTO MANUFACTURING
With breakthrough products that will positively impact the drug delivery ecosystem, a robust manufacturing strategy is also required to support the production. The manufacturing strategy requires an ability to deliver a manufacturing solution that is optimized to what at times can be seen as conflicting requirements. Production of the Companion and Dual Chamber Syringe Systems requires the ability to assemble with extreme precision, allow for continued refinement of the medical device, have the ability to accommodate a wide range of variants, but be capable of manufacturing to scale. Credence partnered with
Mikron, an industry innovator for scalable and customizable assembly solutions, for this unique challenge (Figure 3).
Mikron has extensive experience manufacturing bespoke automation for medical device and pharmaceutical clients. Mikron’s automation philosophy de-risks and enables rapid deployment via the use of standard platforms and subsystem building blocks. This allows Mikron’s engineers to focus more on specific critical aspects of the medical device and assembly process. This automation strategy helped rapidly deploy the lowest possible risk automation solution for Credence – the Flexible Clinical Line (Figures 4 & 5).
COLLABORATION SOLVES THE CHALLENGE OF CONFLICTING CONSTRAINTS
With heritage in the Swiss watch-making industry, developing robust and precision solutions is the norm for Mikron. Mikron has an extensive library of proven sub-system and design standards that can be leveraged to ensure the unique subcomponents of the Companion and Dual Chamber Syringe Systems are assembled and processed to their specifications to ensure patient safety and proper functionality. For the Credence products, this precision includes micro-component feeding, needle handling, precision welding, fine assembly, and vision inspection, just to name a few.
As speed to market is key for a novel product, Mikron needed to concurrently develop the automated manufacturing solutions, while Credence’s design was being refined. This required tight collaboration between the two companies’ engineering teams. As a benefit, some assembly techniques and device component designs were proven out on the Flexible Clinical Line as it was being assembled by Mikron. By utilizing the automation asset to provide real-time feedback, Credence was able to ensure a robust medical device design while Mikron was finalizing the automation.
The ability to accommodate a wide and varied range of products can run counter to automated manufacturing. However, one of Mikron Automation’s standard platforms, the MiniCell, was developed specifically with this challenge in mind. This system provides not only the ability to rapidly deploy automation, but also the unique flexibility that Credence required to manufacture an extensive range of product variations. Credence’s Flexible Clinical Line is a truly unique piece of automation in its ability to produce more than 150 product variants (Figure 6).
With the understanding that the Flexible Clinical Line is one of multiple important steps in Credence’s product manufacturing journey, the two partners are using their experience to influence the design of a future high-volume system to support commercial adoption. This consists of using as many of the processes as possible from the Flexible Clinical Line and leveraging the concept of process equivalency to reduce validation overhead and burden. The teams are also working together to evaluate and refine the manufacturing processes as they look toward the eventual high-speed assembly solution. Through developing subsequent process range capabilities studies and proof-of-principle experiments, Credence and Mikron are together developing the lowest-risk high-volume assembly system that can be deployed rapidly.
SUMMARY
Formulations are becoming more complex, and requirements for the performance and efficiency of delivery systems are becoming more stringent. But the great news is that more effective therapies treating more and more diseases are being delivered in settings that allow patients more comfort. Innovation and collaboration across the supply chain are required to meet the needs of patients and healthcare providers. Credence and Mikron have worked closely together, using creative manufacturing strategies to produce a wide array of problem-solving drug delivery systems. This has been demonstrated with the Flexible Clinical Line’s completion of Factory Acceptance Testing at Mikron and its subsequent delivery to its final destination, where it is undergoing validations required to supply GMP product to Credence’s pharmaceutical customers.
REFERENCES
- Antalfy A, Berman K, Everitt C, Alten R, Latymer M, Godfrey CM. The Adherence and Outcomes Benefits of Using a Connected, Reusable Auto-Injector for Self-Injecting Biologics: A Narrative Review. Adv Ther. 2023 Nov;40(11):4758-4776. doi: 10.1007/s12325-023-02671-2. Epub 2023 Sep 21. PMID: 37733212; PMCID: PMC10567963.
- Companion Staked Syringe Formative Comparative HF Study (CD-003).
- Credence Engineering Report #: ENG-0141.
- https://time.com/collection/time-co2-futures/6691961/companies-offsetting-plastic-waste/.
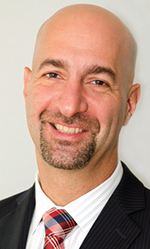
John A. Merhige is Chief Commercial Officer at Credence MedSystems. Previously, he was Vice President, Market Development at Sanofi, having joined Sanofi upon its acquisition of Pluromed. Pluromed developed and commercialized rapid transition polymers delivered from prefilled syringes for use in surgical procedures. Prior, he founded Prelude Devices to identify early stage medtech ventures and gained general management and leadership experience at Ford and Avery Dennison. He graduated from Dartmouth College with a Mechanical Engineering degree and returned to Dartmouth for a Masters in Engineering Management from the Thayer School of Engineering and the Tuck School of Business.
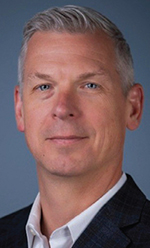
William (“Bill”) Jaworski is the Sales Director and a member of the executive leadership team at Mikron Corporation Denver. Working at the intersection of healthcare, medical device, and manufacturing technology for 20+ years, he has explored market needs and developed solutions to meet those needs as Product Manager, Segment Marketing Manager, Global Marketing Director with GE Healthcare, and as a Business Development Director at ATS Life Sciences. He earned his BS in Mechanical Engineering and graduate degrees (MS in Mechatronics Engineering and a MS in Global Engineering Management) from the Northern Institute of Technology of Hamburg-Harburg, Germany, as well as an MBA from Marquette University.
Total Page Views: 15428