Issue:October 2013
PACKAGING SOLUTIONS - Overcoming the Challenges of Child-Resistant/Senior-Friendly Closure Development in Today’s Changing World
INTRODUCTION
Healthcare packaging has always been a bit of a challenge when compared to other industries. The US FDA has expressed a desire to make 70% of drugs available for over the counter (OTC) use. In an already cautious regulatory environment, industry standards are increasing, bringing additional pressure on manufacturers to provide better child-safe and senior-friendly packaging solutions.1 As the demand for better child-resistant and senior-friendly (CR/SF) packaging is on the increase, so too is the market demand for greater cost effectiveness, sustainability, and value-added end-user benefits. The following will explain how these challenges can be overcome by employing imaginative engineering design and process practices and a healthcare-quality focus.
KEY TRENDS & DRIVERS
The market outlook indicates the future of healthcare packaging solutions will be characterized by constant change, with an expanding market for more convenient and easier-to-use solutions as the worldwide market demand continues to grow. Plastic caps and closures will form the largest worldwide market segment, driven by high value-added designs with enhanced ease-of-use and security features, such as CR/SF packaging and dispensing. Paying attention to market trends and gaining insight from consumers and manufacturers was a key starting point and helped guide the subsequent design decisions to enhance usability of the Clic-Loc® closure – Rexam’s premium CR/SF closure.2
ADDRESSING THE NEEDS OF CHILDREN
Concern in keeping young children safe around medicine is acknowledged by virtually every parent and caregiver’s awareness of the importance of storing medicine out of the reach of young children. However, every year, there are increasing cases of calls to poison centers. According to the 2013 Safe Kids Worldwide report, 86% of emergency room visits for poisoning were due to the child getting into adult medicine. They also state that in 7 out of 10 cases, a child ingested medication belonging to the mother or a grandparent.3
In January 2013, the manufacturer of a popular cold and cough syrup recalled 2.3 million units of product, after four children opened the child-resistant caps and accidentally ingested the medication. According to the US Consumer Product Safety Commission, the federal agency charged with protecting consumers against accident-causing products, the child-resistant caps failed to work in some cases, with children removing the cap even with the tamper-evident plastic seal still in place. “It’s really common,” said Dr. Donna Seger, the Executive Director of the Tennessee Poison Center and a Professor at Vanderbilt University. “Cold and flu medicine are one of the top exposures that children have in the US.”4
Another example of product failing to meet child-resistant closure requirements was the voluntary recall of approximately 898,000 units of a childrens’ pain and fever medication. In this case, the filled container closure system was sufficiently child resistant. However, the accompanying dosage dropper that was supplied with the product was not child resistant, and hence, represented an unacceptable risk.5
In response to these increasing incidences, it has been recommended by several medical and consumer organizations that consumers buy child-resistant packaging when possible and seniors transfer medication to child-resistant packages if children are likely to visit.3
ADDRESSING THE NEEDS OF SENIORS
Due to the aging of the baby boomer generation (born in the late 1940s and 1950s), the American population is getting older. Between 2010 and 2050, the senior population will swell significantly. With the boomer population having reached the age of 65 a couple of years ago, the senior population is projected to reach 88.5 million – well over twice the number of seniors in 2000 and 20% of the total population of the US.
Adults 65 and older spend nearly twice as much as those 45 to 64 on healthcare each year; they spend three to five times more than all adults younger than 65, according to the Center for Disease Control and Prevention (CDC). This increasing elderly population has and will necessitate opportunities for improving quality of life.
The challenge for healthcare manufacturers will be to address the needs of an increasingly segmented market (young, middle, and older seniors); by keeping in mind the differing levels of physical demands and limitations when creating packaging solutions for seniors.
CONSUMER INSIGHTS
Qualitative and quantitative research, lead to the design of a coarse ribbed cap for easier opening and easier closing. Research evaluated the following attributes: time to open, ease of opening, ease of closing, comfort of feel in the hand, ease of following the instructions, ease of knowing the package is closed correctly, overall usage experience, preferred grips (ribbing) on the side of the closures, and readability of the instructions on the closure’s surface.
Consumers overwhelmingly preferred the printed worded, coarse ribbed, and arrows compared to the pictogram versions, with respect to easy opening and closing. When compared to existing CRC closures (ie, closures the subject was already using), Figure 1 shows that 66% of the panel preferred a coarse ribbing version.6
The reasons for this preference given by consumers were primarily linked to ease of opening “bigger ridges fitting better in the hand” and the clearer directions coming from either raised or printed lettering as opposed to pictograms.6
SUSTAINABILITY IS MORE THAN REDUCING WEIGHT
Many healthcare companies are becoming more focused on understanding, measuring, and managing their sustainability efforts. This increased focus has provided a great deal of challenges, as well as opportunity within the healthcare packaging industry. Early on, closure manufacturers addressed sustainability primarily by lightweighting, a practice that reduces the amount of resin used to make the part. Lightweighting, without compromising product integrity, is still important today. However, other aspects, such as reducing energy consumption during manufacturing and material recyclability, play important roles.
Material reduction is not only an efficiency gain. It also reduces transport demands and yields fuel and logistics cost savings across the supply chain. Rexam believes that sharing operational best practices, and applying six sigma and other continuous improvement methods across the organization, helps achieve the vision of best performance both in terms of financial results and environmental records. One illustration of such attention and drive can be shown by this example of recycling plastic waste. Based on a 2011 company report, Rexam cut the tons of raw material per ton of production to 1.14 from 1.15 in the previous year.7
PROCESS APPROACHES CAN ADDRESS KEY CHALLENGES
Increased cost pressures throughout the entire production and packaging process, the increased need to provide tailored individual packaging solutions, as well as a heightened demand for high-quality, defectfree/contaminant-free solutions, are driving closure manufacturers to rethink and simplify their development and manufacturing approach.
THE 3RS OF DESIGN
Although plastic closures are produced in thousands of different styles, they can be classified according to three main molding methods: stripped, collapsible core, and unscrewed. The Clic-Loc® 4 platform utilizes a hybrid approach, the patented 3R (rotating ratchet ring) design was developed by a leading injection molding equipment manufacturer. This innovative unscrewing mechanism is both simple and cost effective. The 3R system allows Rexam to maintain the thread quality of an unscrewed core, while avoiding the maintenance and design compromises of collapsible and/or stripped core parts.
Cycle times are reduced when compared to a standard unscrewing mechanism. This is primarily due to the minimal movement required by the 3R system to clear the threads from the part, and the ability to design-in much more efficient cooling.
The 3R design is also capable of running in standard machines, avoiding the need for capital investment and training on new equipment.
CASE STUDY: REDUCING CYCLE TIMES & COSTS
A 3R mold was compared to a rotating core, both producing identical 38-mm closures. Both molds and hot runners were manufactured by the same supplier and were tested in the same machine, with a reciprocating screw injection unit. All of the process set-up parameters were identical:
• Part weight: 5.0 grams
• Part material: HDPE
• Manufacturer: AutoChem; Number: 2110 MN50
• Color: White; % Concentrate: 3%
• Mold process temperature: 10°C
The 3R mold was able to produce acceptable parts at a cycle time 1.5 sec (18.3%) faster than the rotary core mold. Most of the cycle improvement was a result of reduced hold and cooling time (0.9 sec). The remainder of the improvement resulted from a faster ejection and mold close time (0.6 sec faster).8
IN-LINE MANUFACTURING & ASSEMBLY
The in-line manufacturing process refers to the production work cell. Parts are molded and assembled in one continuous flow as opposed to being molded, stored in a warehouse, transported to an assembly line, and then fed into an assembly machine. Inline manufacturing and assembly can be very helpful when producing closure parts. For example, they are not exposed to contamination from being transported within the plant.
In-line manufacturing can create some major advantages for closures. Any time you can mold parts and feed them directly into an assembly process you create an economic advantage. By molding and assembling inline, savings are driven due to reductions in transportation, storage, waste, contamination, and indirect labor. And the process is inherently FIFO. With Clic-Loc® 4, the parts go directly from the molding machine into assembly via air conveyors.
SHRINK WRAPPING APPLICATIONS
Clic-Loc® 4 is designed with a mechanism that prevents “freewheeling” of the outer closure after application to the bottle. This ensures that the drive lugs between the inner and outer will remain in a “stacked” position during the shrink wrapping process. Figure 2 shows the off-drive lugs of two caps on top of each other in what is known as “stacking position.” The detents prevent the outer from unintentionally rotating counter-clockwise as seen from above relative to the inner cap. Therefore, the off-drive lugs are held above each other and cannot be used to transfer off-torque from the outer to the inner. If top loading occurs on the package or shrink wrap on the neck, the downward force will not cause the off-drive lugs to engage. Therefore, downward force resulting from shrink wrapping will not compromise the CR function of the closure.
OVERCOMING CHALLENGES WITH DESIGN
Decoration Flexibility
Clic-Loc® 4’s outer mold has the ability to remove and replace cavity plates in the press. This allows for different versions of artwork and knurl pattern (ribbing) designs to be changed over without removing the mold from the press. Figure 3 depicts the versatile decoration possibilities, highlighting four potential options.
Capper Flexibility & Variety
Greater tolerance for bigger transfer beads creates greater capper flexibility, allowing one closure to fit variable bottle sizes. Figure 4 shows a section view of the assembled closure on a neck finish that contains a transfer bead below the threads.
Transfer beads can cause the neck to be incompatible with a two-piece push and-turn closure if the transfer bead prevents free operation of the outer cap. Clic-Loc® 4 has been designed to work with many neck finishes that are incompatible with competitive push-and-turn closures due to the elevation and/or diameter of the transfer bead.
Design Effectiveness
Figure 5 shows a close-up of the three concentric V-beads or V-rings (near the center of the image) that provide for a liner-less option feature. The V-ring acts as a sealer, replacing the need for a separate liner, ultimately contributing to cost savings.
The following molded parts are exemplary of the thoughtful approach to achieving the design goals without compromising high quality and performance. Figure 6, shows one of the on-drive lugs/clickers on the inner cap. The lug/clicker is to the left of the annotation in the picture. Above this, one of the off-drive lugs can be seen. Figure 7 shows one of the on-drive lugs/clickers on the outer cap. Below this two of the off-drive lugs can be seen.
THE RESULT OF KEEPING IN MIND DESIGN-FOR-USE PRINCIPLES
Clic-Loc® 4 is the culmination of design enhancements and changes to production processes. Below is a summary of the major improvements.
New Improved Technical Attributes
A top biasing mechanism replaces top spring fingers and keeps CR lugs disengaged. V-rings were added to accommodate liner-less use. Bottle neck finishes with larger max transfer beads can be handled. An overall reduction in height and weight was achieved.
End User & Manufacturer Attributes
A more senior-friendly, easy-to-open closure created in part due to the coarse, ribbing, which runs deeper and wraps around the outer top edge (ie, improved gripability). Able to maintain the warning “click” feedback feature, an audible assist in proper opening and alert to adults when a child tries to open the medicine package. Incorporating an in-line manufacturing and assembly process provides operations economies and contributes to sustainability.
SUMMARY
Rexam Healthcare is 100% focused on delivering high-quality healthcare primary packaging and devices. Healthcare end-users and manufacturers of the products they use are the primary customers. Therefore, quality, manufacturing, and commercial attention is highly concentrated on their needs. Due to its performance, features, and production-line compatibility, the Rexam Clic-Loc® design has earned over four decades of trust and confidence from the world’s most innovative, respected, and demanding healthcare product manufacturers. The design principles incorporated, along with the process improvements, have positioned the Clic-Loc® 4 closure to meet the challenges relating to child safety, enhanced senior usability, cost effectiveness, operations flexibility, and custom packaging. The 38-mm size will be introduced near the end of 2013, followed by other sizes in the range in 2014 and beyond. This latest addition to the premium Clic-Loc® closure family is foreseen to become a standard of care reference for the CR/SF closure market.
REFERENCES
1. New Reality for 2009 Pharmaceutical Market Presented by Diana Conmy, Corporate Director, Market Insights October 2, (2008).
2. Market Trends, Pharma & Medical Packaging (2010).
3. Safe Kids Worldwide: An In-Depth Look at KeepingYoung Children Safe Around Medicine;2013.
4. Triaminic, Theraflu Recalled After Children Accidentally Ingested the Medication. Sydney Lupkin Health Reporter. ABC News;2013.
5. Casey L. Failure to comply with childresistant closure requirement prompts recall. Packaging Digest;2011.
6. Rexam Clic-Loc® Consumer Preference Marketing Research Study;2012.
7. Internal Rexam reports and other documents.
8. Weltonhurst Plastics Blow Moulding Specialists, via the Free Library by Farlex;1996.
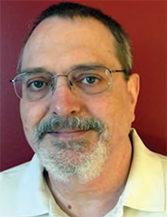
Steve Stalions is a Senior Design Engineer with the Containers and Closures business unit at Rexam Healthcare, a major global player in rigid plastic packaging for the Healthcare market. His responsibilities include the design and development of containers and closures as well as providing customer technical services. He earned a Bachelors degree in Mechanical Engineering from the University of Kentucky.
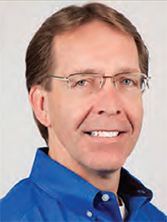
Kurt Attermeier is the Technology Director for the Global Innovation and Engineering Group at Rexam Healthcare. His experience includes over 30 years of product development and operations experience in the medical device and disposables field. He earned his degree in Biomedical Engineering from Marquette University.
Total Page Views: 3834