Issue:May 2024
FORMULATION FORUM - Prefilled Syringes: Overcoming the Challenges for Safe & Accurate Delivery of Drugs
INTRODUCTION
As we continue to discover challenging molecules, the drug industry is open to adapt the innovative methods and technologies for delivery and packaging of new medicines, while keeping top priority in patient compliance, convenience, and easy accessibility to all with an affordable price. Prefilled packaging is a convenient way for precise dosing of parenteral medications. Prefilled syringes filled with liquid formulations, most specifically, offers a wider acceptability among children and aging patient population for self-administrative of small and large molecules for unmet medical needs and life cycle management.1
With continued rise in demand, the market is expected to grow rapidly for ready-to-administer (RTA) prefilled syringes with projected potential market share of $12.8 billion with CAGR of >12% in the next few years.2 This growth is fueled by a surge in geriatric and diabetes populations coupled with increased demands for biologics to address the unmet medical needs requiring the self-injectable route of administration.3 The main interest in prefilled syringes stems from the number of benefits, including patient accessibility and affordability, safety, reducing drug waste, and outweighing patient’s benefit over risk for health providers and drug manufacturers.4 For drug manufacturers, as an example, prefilled syringes can reduce 20%-30% overfilling by accurate and measured fillings, leading to controlled cost. As a matter of fact, prefilled syringes can deliver solution volumes between 0.25 ml and 5 ml; and hence, they are best suited for administering drugs by subcutaneous (SubQ), intramuscular (IM), and intradermal (ID) injections. Coupled with patient risk, safety, compliance, and demands, drug manufacturers are bound to develop in the future more products in prefilled syringes as opposed to traditional sterile vials for injectable medicines.5
The following is aimed to provide a better understanding about some of the advantages of prefilled syringes, methods for manufacturing, and the syringe types commercially available.
ADVANTAGES OF PREFILLED SYRINGES
Prefilled syringes are used due to their conveniences, accuracy, and sterility assurance, mitigating risks in overdosing of drugs, contamination, and dosing errors.6
Convenience
Prefilled syringes leverage convenience to patients and healthcare providers. Because they are a single-use device, they reduce concerns for contamination and overdosing. They allow patients to easily self-administer injection, which is beneficial to patient populations requiring frequent doctor’s visit or requiring daily injection schedules.7
Accuracy
Prefilled syringes provides more accurate delivery of drugs than vial dosing and reduces risk for dosing errors. If dosing is not controlled, it could impact the efficacy of the treatment.8 Yang et al found that prefilled medications for anesthesia, for example, pose far and fewer liability issues compared to self-filled syringes.9
Sterility
Preventing the formulation from microbial contamination is the highest priority in prefilled syringes. It is important to protect patients from undesired adverse effects and/or infections. As a result, the aseptic filling process is used for manufacturing of prefilled syringes for safety and regulatory compliances.10 Once filled, the drug product is sealed off from cross-contamination and remains stable and sterile for 2 to 3 years of its shelf-life. Sterilization is typically done by autoclaving or ionizing radiation. Gamma radiation, usually carried out at 25-50 kGy, is more efficient as opposed to autoclaving. It is also effective for other components used in prefilled syringes, such as plungers and stoppers.11
Manufacturing Benefits
Key advantage for measured filling in prefilled syringes is to avoid excessive filling as is the case with vials and other ampules. For instance, 20%-25% overfill is required for vials or ampules to satisfy the USP recommendation for a typical 0.5-ml fill. In contrast, for prefilled syringes of 0.5-ml volume, only < 2% overfill is needed, as a result, producing 18%-23% more doses for filling PFS than that in vials. Manufacturing prefilled syringes may sound simple, but it could be complex considering the precise control of product viscosity, temperature, pressure, and equipment designs. For example, biologic or protein formulations are temperature sensitive and highly viscous, which could pose challenges in filling the prefilled syringes. Therefore, appropriate aseptic filling strategies are required for handling of these molecules at ambient or sub-zero temperatures without exposure to heat.12
Marketing Benefits
Prefilled syringes offer immediate marketing advantages due to their attractive packaging, less risk, dose accuracy, safety, and self-administrative nature. As a result, dug manufacturers prefer to develop these “ready-to-use” products even with slightly higher marketing premiums. This also leads to broader acceptability by end users, doctors, and healthcare providers. Table 1 shows the approved drugs in prefilled syringe.12
PREFILLED SYRINGE MANUFACTURING PROCESS
Materials & Components Used in Prefilled Syringes
Glass: It is derived from borosilicate glass of hydrolytic class I, stable at temperatures as high as 565°C, but is highly fragile so care must be exercised when used. This is used as a syringe barrel (non-reactive and stable during storage).
Plastics/Polymers: They produce robust, non-fragile devices compared to glass prefilled syringes with better durability, biocompatibility, stability, and lighter weight. They should be free of leachables/extractables to avoid any adverse effects, such as carcinogenicity and immunogenic toxicity. Figure 1 illustrates the components of a prefilled syringe, while Table 2 shows the materials used to construct the prefilled syringe.
Glass filled syringes are of two categories, namely, oil siliconized syringes and baked-on silicone syringes. In oil siliconized syringe systems, there is direct contact of rubber with glass, which leads overtime to higher breakout forces and possible chances of contamination. In baked-on silicone syringe systems, however, there is a consistent coating of glass barrel, which leads to lowering of breakout forces during storage. As shown in Figure 2, where A denotes the higher breakout force (F) in oily siliconized syringes and lower breakout force (F) in baked-on silicone syringes.
In borosilicate glass prefilled syringes (USP Type I), there is a shift in pH as a result from the manufacturing of glass at higher temperature-processing conditions. Sodium borate (Na4B4O7) formed evaporates at 800°C-1000°C, but on cooling to 580°C, sodium oxide remains in the glass on storage, and it releases sodium ions (Na+) in water for injection (WFI) that leads to formation of NaOH and eventually change to alkaline pH in the prefilled syringe.12
In polymer based prefilled syringes, there are 2 types of materials used: Cyclo-olefin polymer (COP) and cyclo-olefin copolymer (COC). These low-density polymers provide high heat resistance, are autoclavable, break resistant, solvent and pH resistant, and transparent and eco-friendly.
There are two types of syringes available commercially. One type is the so-called staked needle syringe in which the needle is pre-attached, and the other type is like a Luer Cone/Luer Lock syringe in which the needle is free and can be attached with the prefilled syringe at the time of use.13 The latter offers the patient advantage of selecting the required needle sizes. Table 3 shows the type of needles used in prefilled syringes for different routes of administrations.
Manufacturing of Prefilled Syringes
Conventional self-filling process requires filling of the syringe with solution and capping followed by sterilization. This filling process may lead to air bubbles. To alleviate these challenges, a bubble-free method is used that involves filling and capping under vacuum involving Hyaluron contract manufacturing technology. By eliminating the air bubbles, it improves the stability of drug from oxidative degradation of sensitive molecules. By placing the stoppers under vacuum, it provides a more accurate fitting in the prefilled syringes.14
Following the filling of syringes, other tests such as sterilization and labeling are required to establish the robustness of the prefilled process. As stated earlier, terminal sterilization is commonly used for sterilization. Autoclaving or steam sterilization is not a probable method as it can lead to package damage and is time consuming. Therefore, gamma radiation is highly preferred.12
SUMMARY & FUTURE PERSPECTIVES
The manufacturing of prefilled syringes involves identifying the components and processing of those materials, including cleaning and sterilizing the container, plunger, needle, and other components used in the assembly process. Once the product is ready, it must be filled aseptically in a sterile clean room with Grade A or ISO 5 laminar flow environments to prevent product from contamination. This is typically done with specialized filling machines designed to control pressure and temperature. Filling is typically done in batches and must be strictly monitored to ensure accuracy. Because the fill and finish process must be conducted aseptically, several considerations must be factored, including use of correct environment and equipment to ensure sterility, maintenance of strict temperature controls, process validation, and environmental monitoring of non-viable and vial counts. It is critical the prefilled syringes are sterile and free of pyrogens. It is equally important the finished prefilled syringes should have complete labeling, packaging, and inspection by visual or automated systems. Improving shelf-life of prefilled syringes compared to traditionally self-filled syringes could help reduce stock losses and healthcare costs. Safety and regulatory compliances will play an important role in the marketing and launch of new prefilled syringes for innovative medicines – small and large molecules, polypeptides, and biologics.
Ascendia has installed a flexible aseptic filler for prefilled syringes, vials, and cartridges within its new state-of-the-art cGMP sterile manufacturing facilities that comply with regulatory standards. Coupled with rigorous testing and quality controls and testing, it is poised to tackle the molecules in the prefilled syringes with novel formulation and aseptic processes that improve a drug’s bioavailability, efficacy, and stability over extended periods. Especially with the emergence of life-threatening diseases like high-stress critical situations or chronic dosing of CNS, oncology, and antivirus diseases, Ascendia is ready to manufacture prefilled syringes for immediate needs. Figure 3 shows Ascendia’s flexible filler for batch size from a few units to up to 30,000 unit/batch.
REFERENCES
- N. Bukanova and H. Tunceroglu, Pre-filled syringes: reducing waste and improving patient safety, Anesthesiologist, 2018, 82, 16-17.
- Soikes, Moving from vials to pre-filled syringe, Pharm. Technology, 2009 Supplement, Issue 5, 1-8.
- Malik, Why utilization of ready to administer syringes during high stress situation is more important than ever, J. Infusion Nursing, 2022, 45, 27-36.
- Dubin, Special Feature- Pre-filled syringes & parenteral manufacturing: Flexibility for faster development, Drug Dev. Delivery, 2019 May.
- C. A. Whitaker and D. K. Whitaker, The impact of using pre-filled syringes on a standard operating procedure for preparing injectable medicines in clinical areas, Anesthesia, 2024, 79, 98-99.
- N. Pagay, R. J. Bachorik, and T. L. Richard, Pre-filled syringe and pre-filled cartridge having actuating cylinder/plunger rod combination for reducing syringing force. Patent Storm: US Patent 5411489 – Pre-filled syringe and pre-filled cartridge, 1995.
- T. Glenn, Prefillable syringes: Trends and growth strategies. Cedar cottage, Newtimber Place Lane, West Sussex, BN6 9BU, United Kingdom; ON drug delivery Ltd; 2006. Registered in England: No 05314696.
- Beele. Increasing Popularity of Prefilled Syringes. Packazine, 2007, 1, 4-5.
- Yang, A. J. Rivera, C. R. Fortier, and J. H. Abernathy, A human factors engineering study of medication delivery process during an anesthetic pre-filled syringes versus self-filled syringes, Anesthesiology, 2016, 124, 795-803.
- P. Jadhav, C. D. Patil, D. D. Sonawane, K. R. Jadhav and K. Salunkhe, Review on prefilled syringe as a modern technique for packaging and delivery of parenteral, Intern. J. Recent Scient. Res. 2020, 11, 11, 38301-38306.
- Mudhar, Are Pre-Filled Syringes the Future? Asian Hospital and Healthcare Management. vol 23. Secunderabad, Andhra Pradesh, India: Ochre Media Pvt Ltd; 2011.
- Makwana, B. Basu. Y. Makasana, and A. Dharamsi, Pre-filled syringes: an innovation in parenteral packaging, Int. J. Pharm. Invest., 2011, 1, 200-206.
- Pironti, M. Raghunathan, and R. Hlodan, Pharmaceutical Online, White Paper, 1-4.
- Danielle, Advanced innovations on a new generation of plastic prefilled syringes. Cedar cottage, Newtimber Place Lane, West Sussex, BN6 9BU, United Kingdom: ON drug delivery Ltd; 2010.
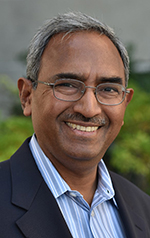
Shauket Ali, PhD
Sr. Director, Scientific Affairs & Technical Marketing
Ascendia Pharmaceuticals
shaukat.ali@ascendiapharma.com
www.ascendiapharma.com
Dr. Shaukat Ali joins Ascendia Pharmaceuticals Inc. as Senior Director of Scientific Affairs and Technical Marketing after having worked in the pharma industry for many years. His areas of expertise include lipid chemistry, liposomes, lipid nanoparticles, surfactant-based drug delivery systems, SEDDS/SMEDDS, oral and parenteral, topical and transdermal drug delivery, immediate- and controlled-release formulations. He earned his PhD in Organic Chemistry from the City University of New York and carried out his post-doctoral research in Physical Biochemistry at the University of Minnesota and Cornell University. He has published extensively in scientific journals and is inventor/co-inventor of several US and European patents.
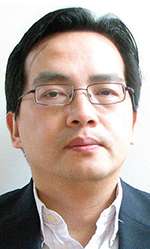
Jim Huang, PhD
Founder & CEO
Ascendia Pharmaceuticals
j.huang@ascendiapharma.com
www.ascendiapharma.com
Dr. Jim Huang is the Founder and CEO of Ascendia Pharmaceuticals, Inc. he earned his PhD in Pharmaceutics from the University of the Sciences in Philadelphia (formerly Philadelphia College of Pharmacy and Sciences) under Joseph B. Schwartz. He has more than 20 years of pharmaceutical experience in preclinical and clinical formulation development, manufacturing, and commercialization of oral and parenteral dosage forms. His research interests are centered on solubility/bioavailability improvement and controlled delivery of poorly water-soluble drugs through nano-based technologies.
Total Page Views: 6519