Issue:January/February 2021
FORMULATION DEVELOPMENT - The Role of Excipient Selection in the Development of Orally Disintegrating Tablets
INTRODUCTION
Orally disintegrating tablets (ODTs) offer multiple benefits to patients that have difficulty swallowing medicines in tablet or capsule form. They can be swallowed without the need for water, making them highly convenient for taking “on the go”. The ability of the active ingredient to rapidly dissolve in the mouth also means they provide a faster onset of action in comparison to other delivery formulations that can be highly useful for products that are required to work quickly such as pain relief medications.
Excipients play an incredibly important role in all formulation development; however, they are even more crucial in ODTs as they can affect multiple characteristics, including taste, odor, and mouthfeel. The following looks at the benefits that orally disintegrating products can bring to patients and developers and assesses the impact that excipient selection can have on the development of successful products.
BENEFITS FOR PATIENTS & DEVELOPERS
There are many patients who struggle to consume standard tablet dosage forms. It can be difficult to persuade young children to swallow them, and they could pose a choking hazard. Adults with a swallowing disorder (dysphagia) or Parkinson’s disease, as well as elderly patients, may also struggle to administer medicines in this form. ODTs present an alternative option that are more easily swallowed and reduce the risk of drug-induced oesophagitis, which can occur when a tablet is caught in the oesophagus and dissolves while remaining in contact with the oesophagus lining. As well as being pleasant tasting, they are easy and convenient to take, and are supplied in a single dose, which removes any need for measuring prior to administration.
ODTs present an ideal platform for active ingredients for the treatment of pain, migraine, allergies, diarrhoea, Parkinson’s disease, insomnia, travel-related sickness, and psychiatric incidents amongst other indications in which rapid dosing and absorption are required. These formulations are also ideal for dialysis patients that need to reduce their daily liquid intake. As well as the patient groups already identified, a significant proportion of the general population finds swallowing tablets difficult, and a disintegrating product can greatly increase compliance. For active patients, they present a useful strategy to take a drug in situations when water is not available, for example during travel or in meetings.
From a development perspective, orally disintegrating medicines may offer excellent bioavailability as they are dissolved and dispersed in the mouth. If the drug is absorbed within the oral cavity rather than digested, it also avoids first pass of the liver. This pre-gastric absorption can reduce side-effects caused by metabolites formed in liver enzymes.
Depending on need and indication, ODTs can offer the option of immediate active pharmaceutical ingredient (API) release, suitable for fast-acting painkillers. They also provide a user-friendly dosage form for many compounds, including poorly soluble APIs. They can also be formulated as fixed dose combinations (FDCs), combining two or more drugs in a single dosage form to increase patient compliance and experience.
MANUFACTURING TECHNIQUES
Orally disintegrating products are all tablets in the sense that they have solid bodies. While some products are manufactured using techniques, including freeze drying, moulding, cotton candy process, and mass extrusion, they can also be manufactured via conventional tabletting technologies, such as direct compression. More advanced technologies are generally patent protected and should only be considered if a less-complex technology cannot offer the necessary product properties.
Most frequently, a conventional compressed tablet technology will be used due to better cost efficiency and a reduced risk of development delays. In addition, this conventional technology offers a better mechanical stability and more packaging options than special techniques, such as freeze drying and the cotton candy process.
The process of scaling-up these techniques for commercial manufacture is also more straightforward than other technologies. Usually, a high-production speed can be achieved. By modifying well-characterized process parameters and varying excipients, a wide spectrum of characteristics can also be achieved via this method in terms of disintegration, dissolution, and mouthfeel.
EXCIPIENT SELECTION
The excipients used for orally disintegrating products can be divided into two groups. These include the usual excipient types that are always required for the development of tablets, such as disintegrates, binders, fillers, and lubricants. Filler selection is important as it is often present in significant quantities and will heavily impact final taste and mouthfeel. Lubricant is even more crucial than in standard tablets as sticking problems are widely associated with these products.
The second group includes excipients that are not normally found in conventional tablets and capsules, such as high-intensity sweeteners (aspartame, acesulfame K, and sucralose), pH modifiers, and flavoring agents. All of these are well established and widely accepted ingredients in pharmaceutical formulations.
A product’s taste should be developed in line with the tastes of the intended patient population. For this reason, it is important that a development team works in close collaboration with their company’s marketing professionals when selecting the flavoring agents. Sugar alcohols and mannitol are incredibly useful in orally disintegrating products due to the contribution of sweetness and a pleasant mouthfeel, as well as favorable technical properties.
Today, the industry is seeing the launch of new and more advanced excipients, with many bringing advantageous properties. These excipients do, however, come hand in hand with higher costs, which will need to be balanced against the benefits that they bring. For example, a more expensive excipient may allow a developer to avoid complex process steps and, therefore, can contribute to reductions in manufacturing costs.
CHALLENGES IN EXCIPIENT SELECTION
In the development of orally disintegrating products, the type and amount of excipient used needs to be carefully identified to achieve the right balance between several technical characteristics. These include stability, dose homogeneity, and dissolution rate. Not less important but more difficult to measure are flavor and mouthfeel. Here, it can be very useful to work with taste panels to ensure that the new product will be appealing to the intended patient population. The use of a Quality-by-Design (QbD) approach and multivariate methods may be helpful. This will result in a better understanding of the optimal process parameters and the robustness of the process. This will also offer the advantages of a more stable process with higher yield and less risk of rejected batches.
FINAL THOUGHT
Orally disintegrating products are gaining increasing attention from the industry by offering distinct advantages in the development of both prescription and over-the-counter medicines. Many studies have already compared these dosage forms with standard tablet forms in vitro and in vivo and have found that orally disintegrating products offer superior compliance and drug solubility. Pre-gastric absorption can also have considerable advantages in terms of both a faster onset of action and a reduction of side-effects.
Successful development of these products requires careful selection of the right excipients. Excipient manufacturers can offer valuable information and support on their products, and wise developers will look to use this insight to their advantage. By taking the time to fully understand how each excipient works in their formulation, manufacturers can ensure they achieve the best selection for their product.
To view this issue and all back issues online, please visit www.drug-dev.com.
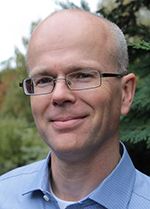
Dr. Torkel Glen is Senior Director, Science & Technology Officer at Recipharm AB. He earned degrees in Pharmacy and Business Administration as well a PhD in Pharmaceutics (Uppsala University). He has worked in the pharmaceutical industry since 1988, and has held a number of scientist and manager positions in Europe and the US. He was lead formulator and co-inventor of Detrol OD/Detrusitol SR. Dr. Glen is Vice Chairman of the Board of the Swedish Pharmaceutical Society.
Total Page Views: 5662