Issue:November/December 2024
DIGITIALIZATION PLATFORM - Breaking Down Communication Barriers in Pharma Manufacturing
INTRODUCTION
A people-centered approach to digitizing manufacturing operations helps ensure the success of any digitalization initiative. But in pharmaceutical manufacturing, having insights into each area of operation is critical to production quality and compliance.
Pharmaceutical operators must be involved at early stages, so their needs and requirements need to be clearly understood. Identifying an enterprise platform that can be configured and customized to meet the needs of end users is key, as well as using an iterative process to ensure optimal configuration for each department and end user.
In a recent LinkedIn post, Jörg Walter, a Senior Manager for Operational Excellence at AbbVie Germany, says “By digitizing our shop floor communication, we not only streamline our processes. We empower our employees to be architects of progress. Their know-how, coupled with state-of-the-art technology, drives our industry forward.”
AbbVie is a global, research-based biopharmaceutical company focused on research and innovation spanning immunology, oncology, neuroscience, eye care and virology, and medical aesthetics. With 50,000 employees, enabling clear communication and aligning operational objectives across shifts and tiers are critical priorities.
Their Ludwigshafen R&D and operations site in Germany employs more than 2,000 people. The facility produces medicines for more than 100 countries. Keeping everything on track requires effective communication and collaboration across teams, shifts, areas of responsibility, and levels of management. However, without centralized systems for knowledge transfer and management, employees faced numerous challenges. Shift handover is naturally highly people- and situation-dependent, possibly leading to loss of knowledge, misunderstandings, and less-efficient action tracking. Information for the site was documented across various systems, making it sometimes difficult to find and use historical data and creating “information overload” for supervisors juggling multiple data streams. Performance information generated by humans and machines was not properly integrated, slowing down improvement initiatives. The seen risk? Loss of knowledge, lower operational efficiency, and a greater risk of failures.
AbbVie in Ludwigshafen, Germany, realized they would benefit from structures and systems in place that would make knowledge more accessible, searchable, and traceable for everyone at the site. They implemented the Shiftconnector enterprise software platform to digitize shift handover and other key aspects of plant process management (PPM). The platform acts as a centralized knowledge management platform and “single source of truth,” streamlining communication at all levels.
SIMPLIFYING COMMUNICATION ACROSS SHIFTS & TIERS
The Ludwigshafen facility runs four shifts for 24/7 operation. One of the key challenges they wanted to improve with digitization was streamlining communications across shifts and roles. They needed a system that would support all relevant operational processes and work for everyone, including shift technicians and supervisors, process scientists and laboratory staff, maintenance, schedulers, and site managers. In addition, they wanted a platform that was usable on any device, configurable for their specific processes and procedures, and fully compliant with FDA CFR 21 and other regulatory standards for GxP and non-GxP information.
To serve as a central knowledge repository, the platform had to bring together both process data (such as sensor data and equipment alerts) and human input (such as shift handover notes and instructions, inspection reports, and observations). Both types of data are required for effective troubleshooting and decision-making.
Shiftconnector brings everything together in one place to streamline knowledge management and transfer. It provides a structured system for shift handover, task management, and process management. Everyone has easy access to both historical data and knowledge and up-to-the-minute notes, checklists, instructions, and observations.
AbbVie in Ludwigshafen now uses Shiftconnector to manage daily operations and drive continuous improvement efforts at the plant in an advanced way. Important information for each shift — such as event logs and temporary instructions — is clearly documented and accessible to everyone, even if they missed the shift handover meeting. Automatic notifications and information transfers keep other departments, like maintenance and scheduling, in the loop.
With the new digitalization platform, tier communication is transparent for all tiers to see live, 24/7. This helps them facilitate communication for shift handover (operator to operator and team lead to team lead), daily review meetings between team leads and production management, value stream meetings (with supply chain, maintenance & engineering, production management, quality assurance, and quality control), the daily huddle for the plant board, and plant walkthroughs by management. The Shiftconnector collaboration dashboard enhances communication both within and across tiers, ensuring issues and questions are escalated up for proper attention and instructions and support filter down to the right people on the floor.
HOW KNOWLEDGE MANAGEMENT DRIVES OPERATIONAL EXCELLENCE
Having a centralized digital platform for knowledge transfer and PPM at the site has significantly increased efficiency and accountability and reduced the workload for shift supervisors. For example, the enterprise platform solution has helped the AbbVie site realize time savings for supervisors on each shift, a decrease in time spent on shift activities and an impactful decrease in nonconformities.
Other operational improvements the AbbVie Ludwigshafen site has seen include:
- Clear communication of tasks and priorities, resulting in fewer mistakes, lost requests, and production delays.
- A structured escalation process to ensure that information reaches the right people for efficient resolution.
- Fewer inquiries from shift operators and other departments because everyone has access to the information and instructions they need.
The AbbVie site credits improved communication and knowledge management for these operational gains. Marcel Weiler, an AbbVie team lead, says “Shiftconnector offers numerous benefits that enhance our daily work. With this tool, we can create tasks and assign them to individuals, resulting in shortened handover times and eliminating the hassle of searching through multiple tablets, documents, or systems. Instead, we have a clear overview of all tasks and instructions, and all crucial information is readily accessible.”
SOLVING THE KNOWLEDGE PROBLEM FOR PHARMACEUTICAL MANUFACTURING
Many pharmaceutical manufacturers struggle with knowledge transfer and alignment across shifts and tiers. And it’s no wonder the typical pharmaceutical manufacturer operates on a 24/7 schedule with three or more shifts, multiple production lines, and many interdependent departments. Smooth operations depend on achieving operational alignment across shifts and organizational tiers and functional areas, including production operations, quality control, laboratory, maintenance, and management. To achieve that close alignment, facilities need to have everyone on the same page with real-time data and efficient transfer of knowledge.
Despite the industry’s complex and high-stakes nature, most pharmaceutical manufacturers still rely on fragmented data systems and ad-hoc communication methods. Essential information for shift handover may be communicated primarily orally during a stand-up meeting, with supplemental notes in a spreadsheet or manual log. Critical production and equipment data may only be accessible to certain people. Calculating key performance indicators (KPIs), such as Overall Equipment Effectiveness (OEE), Batch Cycle Time, or Deviation Rate, often involves complex spreadsheets that are hard for non-technical employees to understand. As a result of this fragmentation, we often see communication problems develop in pharma facilities, including:
Information Silos: Key knowledge is not shared effectively across departments, shifts, or tiers of the organization or not accessible to people who need it. Relevant information may not be shared or is lost in an information overload situation.
Poor Visibility: Information is available, but people do not know where to find it or even that they should be looking for it.
Complexity: People do not understand how to interpret the information or how to apply it to make day-to-day decisions on the job.
When there are breakdowns in communication and knowledge transfer within the organization, several problems can develop, including missed production quotas, quality and compliance issues, safety violations, inefficient troubleshooting, and poor alignment between shifts or departments. This adds up to higher costs, poor customer satisfaction, and a greater risk of legal or regulatory repercussions. Poor communication also impedes continuous improvement efforts, both suppressing the generation of innovative ideas from across the organization and reducing acceptance of and compliance with improvement initiatives.
That is where a digital knowledge management platform like Shiftconnector can help. By bringing both production data and human-generated notes and information together under a single platform, a digital knowledge management platform makes knowledge more accessible, understandable, and usable for the people who need it. That results in fewer human errors and tighter alignment across the organization for increased safety, quality, and productivity.
Digital tools for knowledge management and collaboration can help prevent communication breakdowns and improve alignment and operational efficiency across the organization. To be effective, these tools need to be designed with the needs of 24/7 process industries like pharmaceutical manufacturing in mind. They also need to work for — and with — the people in the organization. Some things to look for include:
- Easy-to-use digital tools for recording and sharing notes for shift handover, equipment inspection and maintenance, and other key facility processes.
- Integration with other plant systems (such as MES and ERP systems) for centralized data management and analysis.
- Data visualization tools that make KPIs and other plant data easily understandable and accessible for non-technical staff.
- Collaboration dashboards for easy transmission of information, directives, and ideas up and down the organizational chain and across shifts and departments.
- Task management and accountability tools to ensure that directives are transmitted to the right people and departments and critical tasks do not slip through the cracks.
- Customization tools so dashboards and other functions can be tailored to the specific needs, language, and processes of the manufacturing facility.
Digitalization in the pharmaceutical industry is about empowering people to do their best work and make better decisions over the day.
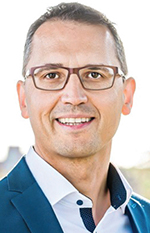
Andreas Eschbach is CEO of the global software company eschbach and inventor of the award-winning plant process management (PPM) platform, innovated Shiftconnector (www.shiftconnector.com) to help production teams streamline shift-to-shift communications and enable a safer and smarter environment through better data sharing and workforce collaboration. Earning a degree in computer science, he draws his practical experience from leading a variety of international software initiatives for major process manufacturing companies, especially in chemical and pharmaceutical industries.
Total Page Views: 2126