Issue:November/December 2023
DIGITALIZATION STRATEGIES - The Era of Technological Transformation in Pharma: Digitalization’s Role in Future-Proofing the Pharma & Biotech Industries
INTRODUCTION
The world is experiencing a technological transformation, which the World Economic Forum has dubbed the fourth Industrial Revolution. As a result, jobs in nearly every industry are experiencing a ground-up metamorphosis to adhere to the digitalization of processes, systems, and skillsets. As a globally operating contract development and manufacturing organization (CDMO), we are not exempt from the impacts of this transformation. CDMOs that embrace digitalization will be better equipped to meet the evolving needs of their customers with minimized human error compared to those who avoid change. Though many may see digitalization as a threat to job security, we are valuing the nexus between human-driven innovation and the support of improved digital processes. Through this embrace, we enhance our business’s capabilities to produce life-saving medications for patients around the world.
As digitalization becomes a cornerstone for businesses that will see success in the future, our customers have expressed gratitude for our reliability and up-to-date nature. Although digitalization is a worldwide trend, the way it is implemented in the pharma and biotech industry is unique. In addition to the complex requests and expectations of our customers, the requirements to protect the sensitive and fragile nature of high-value molecules are also increasing. Together, this results in a highly volatile environment amidst the evolution of the industry.
Organizations that keep up with the technological transformation and incorporate employees in new digitalization strategies can likely achieve the greatest-possible success. This can be driven by the ability to produce high-quality drug products, and the commitment to reskilling employees, bringing human-centric value to an increasingly tech-driven industry. We, among many other CDMOs and pharma/biotech companies, are adapting to digitalization in several ways that not only adhere to our models but enhance our capabilities.
OPTIMIZATION AS AN IMMEDIATE UNDERTAKING
As referenced by the World Economic Forum, digitalization is happening now, with an estimated 1 billion jobs expected to be transformed by technology by 2030. Companies that strive to be progressive, a foundational value at our company, are seeing this change and making internal adaptations accordingly. CDMOs, in particular, have several areas where digitalization improves processes, from administration, to production, quality control to logistics, and more. As with any transformation, digitalization is an ongoing evolution, and as such, companies must commit to making constant changes – this change will not happen overnight and will not stop at one or two changes. Rather, it will be a continuous process that could likely go on for decades.
We place a strong focus on the quality and success of our projects in Production, Quality Control, and Industry 4.0, all of which are managed by a digitalization strategy that is several years in the making and continuously adapted as necessary. To further enhance our digitalization, technologies like the Internet of Things (IoT), virtual reality (VR), and autonomous, collaborative robots have been incorporated into our approach. For example, Helmo and YuMi, two kinds of robots that we have integrated into our production processes, have improved the time and quality of tedious work, allowing human employees to redirect their focus to process steps where the work of employees creates a higher impact. Helmo is a mobile robot system that works autonomously and can navigate diverse working environments to successfully complete technical tasks, for example, the thawing of previously frozen drug solutions.
Similarly, YuMi (aka You and Me) serves as a partner to add flexibility to assembly processes for individualized products, enhancing workflow precision. Although many view robots as a risk for heightened job displacement, we have experienced and clearly communicated the opposite right from the start. Robots serve to improve the work outputs of humans, by taking on repetitive tasks and allowing more time for people to focus on specific conceptional work. In addition, YuMi must be trained by humans to adequately be able to accomplish packaging tasks, leaving room for technology and humans to collaborate side by side.
THE HUMAN ELEMENT OF TECHNOLOGICAL TRANSFORMATION
Although the result of digitalization appears to be less of a need for human support, achieving this result requires the opposite. Our digitalization strategy is built on the foundation that people drive the evolution of processes. Transforming to adapt to new technologies requires human understanding of complex and highly regulated production processes to find proper technological solutions that enhance them, without negating the high levels of quality that our customers expect.
For us, digitalization is truly human-driven. Our colleagues evaluate current processes for gaps or areas of improvement and in turn, find new appropriate technologies that solve these problems without sacrificing anything from the resulting injectable drug product. The result is a seamless collaboration between people and supporting technology.
Additionally, we have developed a Digital Transformation strategy to define the guard rails for digitalization across our global company.
NAVIGATING NEW CHALLENGES
As with any industry-wide change, and in particular, global revolutions, digitalization does not come without its challenges. Though positive results are already proven, and the potential of these new digital processes are seemingly limitless, navigating this new, tech-driven work environment brings unprecedented obstacles. All employees must be aware of these obstacles so they can address them in an efficient and timely manner.
By incorporating the teams that will work with new technology into the planning and strategic development process, companies can proactively address concerns and instill a sense of collective responsibility for the success of these processes. Further, this early inclusion allows company leadership to address fears of job displacement head-on, and to provide assurance that digitalization is a tool to support employee success.
THE PATH FORWARD
Digitalization is already underway in nearly all industries around the globe. As a leading CDMO, we have chosen to accept this transformation with open arms to evolve with the times and continue striving to provide our customers the highest quality, best time-to-market, and most effective processes for manufacturing their life-saving drug products. This flexibility to adapt to new innovations is engrained in our company culture, in which we want to serve as a reliable, progressive, and responsive partner to small and large renowned pharma and biotech companies producing life-enhancing medicines. While digitalization is not the answer to every process within our company, it does serve several purposes where we see added value. It is in those spaces where we are integrating new technology to support sustainable growth for years to come.
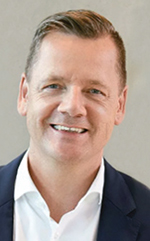
Kai Vogt is Senior Vice President Corporate Development, Legal & Compliance, IT, Vetter Pharma-Fertigung GmbH & Co. KG, where he has managed the Corporate Development, Legal & Compliance as well as IT departments since October 2016. Following a commercial apprenticeship and studies in business administration, he assumed operational and strategic responsibility in both industry and consulting. Before joining Vetter as a Senior Manager, he was responsible for international business development at centrotherm and Bilfinger Industrial Services. In cooperation with his team and the various departments within Vetter, he advances the implementation of the company’s strategy and, among other responsibilities, the digitization of Vetter’s core business.
Total Page Views: 3281