Issue:September 2021
DIGITAL CUSTOM PLATFORM - PCI Pharma’s Digital Transformation: Reaching New Levels of Customer Experience
INTRODUCTION
Approximately 2 years ago, we began to incorporate digital transformation as core to our business strategy at PCI. This decision was based on increasing evidence that investment in digital solutions provides real and measurable returns. And now, digital transformation is a key differentiator for us as we work to build even more collaboration and efficiency across our global organization.
NOVEL DIGITAL PLATFORM PROVIDES REAL-TIME VISIBILITY
As part of our 3-year digital strategy, this past year, we launched pci | bridge – an innovative, first-of-its-kind digital customer platform designed to transform the customer experience. pci | bridge is all about transparency. It gives our customers immediate, real-time visibility and tracking of their clinical and commercial supply chain, which allows for greater collaboration with PCI’s teams, along with instant data and insights to inform decision-making.
The platform technology closely and securely integrates PCI’s systems for customers so that the supply chain can be managed from both sides while eliminating time-intensive manual processes. It works by connecting many different technologies at multiple sites and presents data through an easy-to-access, simple industry-leading interface. With clinical trial management, for example, the platform helps customers better manage that process from beginning to end, from shipments to temperature control, with seamless functionality. While pci | bridge is currently focused in our commercial and clinical trials business, we plan on introducing it on the manufacturing side in the future.
COMMITMENT TO TRANSPARENCY: MANUFACTURING SERVICES & RECENT EXPANSIONS
Looking at our technology on the manufacturing side, PCI’s commitment to transparency becomes clear. Transparency is essential for quality control and accuracy, particularly with our specialized high-potent processing equipment. The operation must be repeatable as per the defined specification to ensure that medicines are accurately produced with no cross-contamination. With unparalleled capabilities and experience in the contained manufacture of highly potent compounds, our Tredegar site in the UK excels as PCI’s center of excellence for drug development and manufacture.
Significant investment in cutting-edge technologies and world-class award-winning facility design has enabled a truly market-leading service for the development and manufacture of highly potent clinical- and commercial-scale products. Services provided out of Tredegar for our global clients include formulation and analytical development, clinical trial supply, and commercial manufacturing of solid oral dose, powders, liquids and semisolids, supported by in-house packaging and labelling services and on-site testing and release services.
In early 2019, we completed a significant investment to double our tableting capacity at the existing contained manufacturing facility (CMF) at Tredegar due to the increased need for high-potent manufacturing we had seen throughout the past few years. In 2020, we also expanded our analytical services by 30%, building a three-story bespoke facility, increasing capacity to deliver capabilities including method development, method validation, stability, and analytical release testing to support ongoing growth in high-potent manufacturing requirements.
As the market continues to grow, we’ve seen an increasing number of clients look to us to provide manufacturing services across the spectrum of dosage forms. To keep pace, we are building a second CMF due for completion in early 2022. When the original CMF (CMF 1) was opened in 2013, just 25% of new chemical entities coming into market were classified as high potent; now it’s more than 40% with no signs of slowing. CMF 2 will replicate the original facility, in effect doubling processing operations in terms of dispensing and fluid bed granulation of high-potency products at both the clinical and larger commercial scale. It is also worth noting that soon after the opening of the original contained facility, additional investment was made adding contained roller compaction technology to support clients in need of development and manufacturing services for highly potent products sensitive to heat and moisture. This ensured that we were able to offer the full spectrum of wet and dry granulation techniques for such specialized potent products.
While many companies involved in the processing of highly potent molecules may use traditional methods and personal protective equipment (PPE), our safety is primarily achieved through engineering design. Operations are conducted using fully contained engineering technologies to protect workers and the environment, which also gives operators more dexterity and control when operating the equipment. The processing technology is managed via a digital interface, considered leading edge.
The Tredegar expansion will double our large-scale manufacturing capacity to ensure that new and existing customers have their development and supply needs met both now and in the future. These investments in Tredegar are part of our ongoing business strategy to remain flexible in an ever-changing marketplace to better service our clients who require a supply chain partner able to deliver an end-to-end service, from drug development to commercialization.
In the US, we have seen a swell of activity from biotech companies on the West Coast in early stage compounds, and we have a strong interest in working with them, so it makes good strategic sense to add early stage manufacturing capabilities in this area. We are exploring the option of adding such early stage manufacturing services at our San Diego site to complement ex-US manufacturing services. Currently at the Tredegar center of excellence, we are able to offer micro-dosing Xcelodose® technology for early phase proof-of- concept activities. Xcelodose® delivers drug directly into capsules or vials, removing the need for initial formulation development and associated stability, and leading to faster first-in-man studies and cost efficiencies. The fully programmable system ensures exceptional levels of accuracy and precision while minimizing drug substance waste.
DIGITAL PROCESSES, MONITORING & QUALITY MANAGEMENT
When we look specifically at the manufacture, distribution, and packaging of high-potency materials from a digital perspective, the equipment is highly complex and computerized. We have a validation team trained in testing of the computer systems, which further increases the level of confidence of the operations team. The computer systems help us follow the latest compliance guidelines and quality regulations. We also ensure that we have the most up to date batch report systems and process manager technology, so that when we conduct our commissioning activities, especially toward new facilities, we know that our teams have received all relevant training on compliance guidelines.
Because additional batch reporting is needed with tablet compression machines, we have also invested in fully automated online process checking technology so that at any point in the process, the team can simply check the human machine interface (HMI) screen. The benefits include real-time monitoring of variations in tablet parameters against a defined specification, and can allow for accurate and fast modifications. And from a commercial standpoint, we have the capabilities to run the machine in automatic modes, ensuring an efficient process.
Our high-potent granulation and fluid bed drying technology utilize a process manager system for recipe management, data recording, batch reporting, security synchronization, and electronic signature control. In addition, fully automated wash recipes ensure robust and repeatable performance for routine and high-containment potent products.
Other critical aspects of our process are our Building Management systems (BMS) and Environmental Management systems (EMS). PCI Tredegar uses EMS to monitor ISO 8 cleanroom environmental conditions with all EMS systems being fully validated and calibrated to monitor critical environments at all times. The systems are 21 CFR Part 11 compliant, which requires that all system data is auditable, password protected, and fully secure. Alarms indicate when any of our environments are outside their specified limits. We use both hard wired and wireless telemetry systems to monitor all critical environments on site. The systems are fully calibrated, and all EMS probes are certified to be within their specified accuracy. The systems are also set up to automatically send emails to departmental managers in the event of an alarm activation, and are monitored by appropriately trained staff when the site is unmanned. The EMS and BMS systems demonstrate that the ISO 8 cleanrooms operate within their correct temperature, relative humidity conditions, and pressure differentials.
The next steps in our digital evolution are to go fully electronic with our batch documentation.
THE FUTURE
For the future, we are looking forward to seeing the results of our digital transformation touch all pillars of our business from manufacturing to clinical to commercial. We are confident that our digital and technology strategy will deliver new levels of customer experience and differentiation, as we are already seeing the significant value our new digital processes are creating for our customers and business. As PCI continues on its digital transformation journey, challenging the status quo and listening to our customers as we go, we are enhancing all aspects of our operations to get life-changing treatments to patients faster.
To view this issue and all back issues online, please visit www.drug-dev.com.
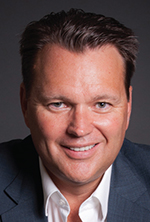
Wayne Hull is a Digital Transformation Global Leader, strategizing and operationalizing digital value at scale. His current global leadership role in PCI Pharma Services, a global pharma supply chain leader, includes Digital, I.T., and Marketing across North America, Europe, and Asia Pacific.
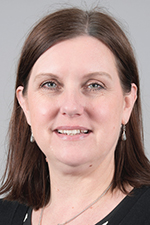
Dr. Rebecca Coutts graduated from the University of Bath, UK, with a Bachelors in Pharmacy before earning her PhD in Pharmaceutics from Cardiff University. She is also a registered member of the General Pharmaceutical Council. Over her 25-year career, she has shown a clear passion for development services and currently holds the role of General Manager for PCI Pharma Services Tredegar site, PCIs center of excellence for manufacturing services. Prior to this, she held roles including Director of Development for the site with specialist expertise in the development and processing of highly potent molecules and Associate Director of Contained Manufacturing. Before joining PCI, she held multiple roles, including Head of Pharmaceutical Development for Vectura and Group Leader, Manufacturing, Science, and Technology Services at Abbott Laboratories.
Total Page Views: 3278