Issue:September 2023
DEVICE DEVELOPMENT - Connected Auto-Injector Development: How to Leverage Human Factors Engineering
INTRODUCTION
Drug delivery devices, such as auto-injectors, that allow for patient self-administration of medication, always need to ensure safety and effectiveness, whilst also, whenever possible, maximizing comfort and convenience. Connectivity adds a new dimension to these essential elements as connected drug delivery devices can capture, transfer, and display injection data, providing the user with step-by-step feedback during the injection process and reminders about future doses.
While providing a whole range of benefits, however, connected devices can also pose new challenges. Manufacturers must find a balance between offering users “enhanced” functionality whilst ensuring the added “bells and whistles” do not increase complexity and hinder ease of use. Early human factors engineering helps ensure user requirements are captured and fed into early design decisions that shape the way connectivity is managed in the medical device user interface.
Regulatory agencies also increasingly stress the importance of incorporating human factors and usability engineering throughout the design and development process. A thorough human factors process is a key constituent for regulatory submissions. In the US, for instance, the US FDA is currently reviewing the content of human factors and usability engineering standards and guidance as part of US marketing authorization.1
This combination of considerations is understandably making human factors analysis and user studies crucial to the advancement of connected drug delivery devices design and successful regulatory approval. The following will examine the human factors process for such devices, including a detailed look at Owen Mumford’s recent development of the UniSafe® 1 mL auto-injector.
HUMAN FACTORS STUDIES AT A GLANCE
Formative and summative user testing is the best known and perhaps most feared aspect of the human factors engineering process. However, there are some key preliminary activities that must precede any user testing in order to optimize the user interface and lay the foundation for successful user testing plans and outcomes.
Preliminary activities are geared toward getting the best understanding of the intended users and their strengths and limitations, the intended context of use, and intended use scenarios. Early user research around these topics also seeks to understand the known use issues with similar devices on the market. As early concepts and ideation start to formulate, these activities help to inform the first draft of a use-related risk analysis (URRA). The URRA helps to inform and shape requirements for the user interface and continues to develop and iterate alongside the device concept. Critically, it is central to the human engineering process and helps to drive any user interface evaluation planning during the design and development process right through to validation.
The human factors testing process involves both formative and summative studies to evaluate the intended use of a device, test the product in the intended use environments, and ensure its suitability for different user groups. Participants are recruited to resemble intended users as closely as possible, incorporating the range of most pertinent characteristics, such as age, gender, training levels, reading age, physical and sensory impairments, and previous experience.
In formative tests, the product is put into the hands of intended users early in the development process to ensure the concept is sensitive to their needs. This also helps to ensure there is sufficient time to shape the design interface and mitigate potential use errors. As the fidelity of prototype(s) grows, intended use scenarios can be simulated more closely. Formative testing should be revisited until satisfied that no further design mitigations are required. Finally, a summative test is carried out on final product equivalents of all aspects of the user interface to confirm and demonstrate the device is safe and effective for intended use.
UNISAFE 1 ML AUTO-INJECTOR
Although Owen Mumford Pharmaceutical Services has been developing auto-injectors for more than 35 years, the UniSafe 1 mL auto-injector is the first drug delivery device incorporating connectivity. With the ability to incorporate fill volumes of between 0.1 mL and 1 mL, the device aims to support patients managing a wide range of conditions, encouraging adherence to treatments and providing healthcare professionals with access to treatment data. Minimizing the risk of needlestick injuries – a requirement for all needle-based devices – was achieved by using the UniSafe sharps protection feature, with the UniSafe safety device being inserted into the autoinjector prior to use. This also ensures the device prevents needle exposure before and after the injection process. The team also simplified user steps during injection by incorporating the priming function for drug delivery into the device open/close action.
UNISAFE AUTO-INJECTOR: DEVICE DESIGN & TESTING PARAMETERS
Alongside design engineers, the human factors team looked to find a balance between providing a simple and effective user interface while still accommodating technical solutions. Emphasis on ergonomic design incorporating anthropometric data allowed developers to shape the physical interface. Psychology of user interface design contributed to key decision points around the Bluetooth connection process, placement of Bluetooth button, and power management; a key user requirement was that the added functionality should not influence a safe and effective injection procedure.
Human factors testing on the UniSafe 1 mL auto-injector was specifically conducted to work under a worst-case use scenario. Although patients would most likely be introduced to device components by a healthcare professional, those in the study interacted with the device with no training and with no direction to read instructions before use. This allowed the team to gain an understanding of how patients were handling devices, understanding the display and controls, and interpreting the signals of connectivity before any guidance had been provided.
The human factors team looked to conduct studies on each aspect of the digital interface as soon as an acceptable level of reliability was reached. The smartphone application to go alongside the device could quickly be generated and simulated in Adobe XD before writing the software. However, device components and electronics, including the ability to connect the device, developed at a slower pace.
UNISAFE AUTO-INJECTOR: LEARNINGS FROM TESTING
Formative studies helped to evaluate the content and flow of the app and reinforced Owen Mumford’s commitment to developing a “demonstrator” app to support safe and effective injection practices. As the app evolved, there was inevitable disruption to the process caused by the differing speeds of development of other device components. As a result, the team mimicked connectivity in the app during studies to get the most out of testing.
The human factors process also allowed Owen Mumford to develop generic instructions for use (IFU) in an appropriate format for users and align with potential packaging options. The best solution appeared to be a landscape booklet, allowing enough space to present intended user steps. Moreover, the team also experimented with different colors on the key touch points to guide loading and unloading of the device. This showed the impact of different colors on the user experience whilst allowing the team to assess different aesthetic and marketing proposals.
SUMMARY
Incorporating connectivity into drug delivery devices is a challenging process. Whilst there are a number of exciting possibilities, developers must create devices that remain user friendly while harnessing the latest technologies. Extensive iterative human factors studies – of both the physical and connected interfaces of a device – ensures the device design is optimized for different user groups by the time it is ready for commercial launch. u
REFERENCE
- FDA (2022). Content of Human Factors Information in Medical Device Marketing Submissions. https://www.fda.gov/regulatory-information/search-fda-guidance-documents/content-human-factors-information-medical-device-marketing-submissions.
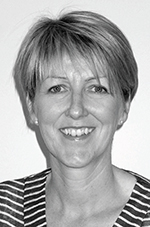
Finola Austin is Human Factors Lead at Owen Mumford Pharmaceutical Services. Aa a highly experienced Human Factors Engineering Manager, she boasts 15 years of experience in mentorship and management of human factors services in safety-critical industries. Her career began in Occupational Therapy within acute, long-term and community settings, and her training in accessibility has given her special insight into the needs of impaired users. Since then, she has successfully planned and delivered Human Factors activities for hundreds of hand-held medical devices, including auto-injectors, emergency use devices, inhalers, injection pens, and lancets, and is proficient in the generation and review of documentation. She has executed numerous user evaluation studies in the UK and US – including studies on safety engineered devices, injection pens, and color differentiation.
Total Page Views: 3482