Issue:October 2019
DATA ANALYTICS - Leveraging Cloud-Based Data & Analytics to Optimize Pharmaceutical Manufacturing
INTRODUCTION
A pharmaceutical product’s life cycle can be broken down, broadly, into three phases: clinical development, manufacturing, and commercialization. Increasingly, the life sciences industry is applying data analytics to clinical development to yield productive business insights that positively influence the drug development process. Analytic solutions are also being leveraged to optimize and inform marketing activities, including patient and HCP support and outreach. Bookended between clinical development and commercialization, manufacturing stands apart as an area that has remained largely untouched by the power of data analytics. That is starting to change.
Analytics in relation to operational efficiency has not traditionally been a focus area for biopharma. Life science companies are, by nature, innovators, so it makes sense that applications of data and analytics have, to date, primarily been applied to the discovery and development of therapeutics, as well as the creative marketing process. However, recognition is increasing about the powerful impact data and analytics can have on optimizing the manufacturing process and ensuring demand is met every time, all the time. A trend toward leveraging cloud-based technology to inform the visual factory has begun, and it is increasing manufacturing efficiency and productivity.
THE VISUAL FACTORY
The concept of the visual workplace, or factory, is a continuous process improvement paradigm that is an outgrowth of the Lean production process pioneered by Toyota in the late 1980s. A key concept of Lean process thinking is the elimination of Muda, the Japanese term for wastefulness or uselessness. A visual factory leverages visual representations of information, such as signs, charts, graphics, and other images, for quick dissemination of data within a Lean manufacturing process. The current status of all manufacturing procedures is thereby immediately apparent and accessible to all who need them. Time and resources needed to convey critical information are minimized, eliminating waste, but the availability and resulting impact of having that information readily available positively impacts the entire manufacturing flow. Streamlined communications yield maximum productivity, including:
-Reducing workflow problems, increasing product quality and productivity, as well as improving communication.
-Improving workplace safety by eliminating hazards and establishing compliance to work standards.
-Aligning employee efforts with goals and strategies for eliminating waste.
ANALYTICS & THE VISUAL FACTORY
Like most other industries, life science companies do their best to create efficient manufacturing operations, regularly reviewing, updating, and modernizing processes and procedures. However, according to McKinsey & Company, this is not enough:
“There’s one significant asset that manufacturers have not yet optimized: their own data. Process industries generate enormous volumes of data, but many have failed to make use of this mountain of potential intelligence. Historically, manufacturers have lagged other industries in their IT capabilities. However, thanks to cheaper computational power and rapidly advancing analytics opportunities, process manufacturers can put that data to work, gathering information from multiple data sources and taking advantage of machine learning models and visualization platforms to uncover new ways to optimize their processes…”1
Data analytics can streamline manufacturing operations and provide extremely focused and actionable insights that enable production line adjustments for inefficiencies related to issues as varied as machine down time, set-up time for lots, optimizing staffing mix, and shift changes. Results translate into minimized deviations to plans, in addition to time and cost savings. These outcomes are, to a large extent, technology agnostic. They are not reliant on one particular platform or solution, but rather can be addressed by any qualified cloud-based data and analytics technology that accelerates and connects disparate sources of data. Such real time and big data analytics essentially enable manufacturing systems to assess and identify their own correction needs.
In particular, there is a current trend for data and analytics to inform four main areas related to the concept of visual factories:
Measure & Monitor in Real Time: Cloud-based data and analytics technologies facilitate real time visibility to predict and propose immediate actions to ensure quality and make the manufacturing process more robust.
Solutions to Meet Unique Needs: Data and analytics not only help identify the unique, specified needs of individual factories, they support the formulation of tailored solutions. Facilities and lines manufacturing injectables clearly have different prerequisites and needs than those producing solid dose tablets. Preconfigured packaged functionalities covering usual, but hard-to-solve, industry requirements may not fit most facilities.
Qualified & Regulatory Compliance: Data and analytics platforms require continuous qualification to ensure the traceability of information and its data sources using regulated frameworks with specific solutions designed for this purpose. This process is imperative and must be respected.
Analysis & Knowledge Discovery: The approach used by a cloud-based data and analytics platform to find relationships between data, combined with the power of real time and big data analytics, enables customers to discover new optimization paths.
These trends ladder up to the objective that is at the heart of any application of cloud-based data and analytics to the manufacturing process: simplifying factory operations. To achieve this goal, it is crucial to adhere to several guiding principles:
Start Simple: Keep the complexity low and demonstrate proof of concept and impact early on.
Focus on the Important Measures: Identify key performance indicators (KPIs) without being distracted by extraneous influences.
Identify the Change Drivers: These will guide process improvements.
Monitor Visually on the Factory Floor: Customizable, real time alerts will enhance functionality, productivity, maintenance, collaboration, safety, and communication.
Prove it Works: Outcomes are key, so adhere to KPIs.
Remember That People Drive Changes: Analytics are designed to provide information that ultimately impacts human behavior. What use is valuable data unless it spurs someone to action?
Saama Analytics has developed the following summary of Meaningful KPIs for cloud-base analytics in the manufacturing process (Figure 1).
Saama recommends that each area of the manufacturing floor be governed by only the most relevant KPIs for that particular part of the manufacturing process. No more than 5 to 7 metrics should be made available visually per area, to ensure that the right analytics are reaching the right people at the right time. Saama deploys its Fluid Analytics Engine (FAE) to deliver scalable, cloud-based, advanced analytics solutions for manufacturers. Using a standards-based technology stack, FAE drives faster ROI and rapid time-to-market for modern analytics with flexibility and adaptability. As part of its core analytics engine, Saama’s FAE includes data connectors and crawlers, security integrations, data models, data processors, advanced analytics integration, and visualizations. Such a potential visual factory solution framework is depicted in Figure 2.
Business needs drive all aspects of a biopharma operation, including user-centric visual analytics. Such analytics engage users, reduce risk, and accelerate time to value in the visual factory, as depicted in Figure 3.
SUMMARY
The data analytics-informed visual factory represents an exciting future for the manufacturing process. Simultaneously, it is also a stepping stone to the future; specifically the factory of the future – a manufacturing process in which every element of product production is guided by artificial intelligence and machine learning (Figure 4).
Until the factory of the future can be realized, however, the cloud-based visual factory can offer the life sciences industry as-of-yet untapped and unrealized competitive and economic advantages. By leveraging data analytics to fulfill product manufacturing demand every time, all of the time, biopharma companies will ensure that resources are efficiently deployed, inventories are optimized, and customer demand is met.
REFERENCE
- https://www.mckinsey.com/business-functions/operations/our-insights/manufacturing-analytics-unleashes-productivity-and-profitability.
To view this issue and all back issues online, please visit www.drug-dev.com.
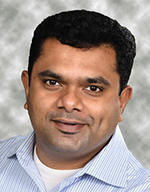
Benzi Alex Mathew is VP & Partner at Saama Analytics, and has been focused on the Life Sciences industry for almost two decades – trying to reinvent ways to help drive efficiencies through IT that helps Life Sciences companies reinvest savings into innovative new cures and improving access to affordable therapies for millions of patients. He and his teams are currently working with Pharma and Biopharma clients executing Analytics Innovation Lab experiments exploring the use of AI/ML, Data Science, Virtual Intelligent Assistants, Cloud Technologies, RPA, and Real World Analytics in the Commercial, Clinical, Manufacturing, HR, Finance, Legal, and IT functions. He is currently focused on setting up the Next-Generation Data & Analytics Operations model for Life Sciences companies to drive value 10x faster, better, and cheaper by integrating Data-Dev-Ops using modern technologies. Mr. Mathew is based out of Saama Analytics’ Silicon Valley headquarters in Campbell, CA.
Total Page Views: 4075