Issue:June 2024
CONTAINER PLATFORMS - Ready-to-Use Containers: Real Benefits, Important Challenges & Evolving Value
INTRODUCTION
With injectable drug products, there are many different factors that must be carefully evaluated to develop an optimal aseptic manufacturing strategy. Among these many considerations, there is one critical decision that every CDMO can help their customer navigate: Which aseptic filling line is right for the product?
Container type has historically been one of the most decisive factors, as aseptic filling facilities have long relied on container-specific platforms designed to process bulk vials, syringes, or cartridges sterilized on-site. Today, however, a growing number of drug developers and drug manufacturers are shifting their attention to ready-to-use (RTU) container platforms: increasingly format-agnostic systems that process pre-sterilized containers delivered in fill-ready nest/tub or tray configurations. These platforms offer an added level of flexibility and efficiency that has made them a desirable option for many injectable drug owners.
As a result, weighing the benefits of bulk and RTU container platforms has become an important step in developing an aseptic filling process. Each system type offers key benefits that are valuable for CDMOs and their customers to consider together. The following will look closer at some of those key benefits, dynamics driving the adoption of RTU container platforms, and several important areas of continuing evolution in the RTU market.
RTU ADOPTION DRIVERS
RTU container platforms are playing a fast-growing role in the global value chain for sterile injectables, with a projected value of $943.5 million USD by 2029 and a predicted 8.2% CAGR from 2023 to 2029.1 Several factors have contributed to this market’s growth:
Development Timelines: Today’s drug developers face increasing pressure to get new therapies to market as quickly and efficiently as possible. RTU container platforms eliminate several time- and cost-intensive steps in the typical development cycle for sterile injectables, such as qualifying a sterilization process and developing a siliconization process for syringe- or cartridge-based products. Adopting these systems has become a valuable way to accelerate new products’ overall path to market.
The COVID-19 Pandemic: The global surge in demand for COVID-19 vaccines also drove a spike in demand for systems that could be quickly and efficiently configured to process these injectable products. At the same time, this shift also created substantial demand for resources that could be swiftly adapted to process products displaced from their filling lines to make room for COVID-19 vaccines. Over the last several years, adopting RTU container platforms has been a valuable approach to addressing these related needs.
Diversifying RTU Container Formats: RTU container platforms have been in use for decades, but have historically been focused on processing pre-sterilized syringes. In recent years, suppliers have greatly expanded the range of container formats that these platforms can leverage. This step has made RTU container platforms a feasible option for a much wider range of injectable therapies, and a valuable resource for drug owners who want to maximize production flexibility across their products’ life cycle.
Together, these dynamics and developments continue to drive both interest and investment in RTU container platforms – while also expanding the range of scenarios in which those platforms can be the right choice for a sterile injectable.
At the same time, however, conventional bulk filling lines continue to offer valuable benefits that CDMOs and their customers carefully compare with the advantages of an RTU-focused filling strategy. Let’s take a closer look at these important considerations, and how they can inform an optimal choice of aseptic filling line.
FINDING THE RIGHT PRODUCT-PLATFORM FIT FOR A STERILE INJECTABLE
Depending on several factors – including market size, life cycle strategy, and more – both bulk and RTU container platforms can offer valuable benefits to consider when selecting an aseptic filling approach. Here are some important examples:
Bulk Container Platforms: These well-established platforms are typically optimized for a single container type: vial, syringe, or cartridge. Many bulk container lines can also be readily adapted to many different variations of the format they process, enabling streamlined adjustment to different suppliers’ containers.
With today’s production technology, bulk container platforms are often an advantageous choice for vial-based products – particularly those with bigger production volumes. Vials frequently come in larger sizes, which reduces the number that can be placed in a tub of RTU containers and limits the speed at which pre-sterilized vials can be filled. Processed in bulk, this format is also typically easier to check-weigh without reducing line speed.
At the same time, bulk container platforms require both sterilization processes and infrastructure, such as washing areas and dry heat tunnels – all of which can add substantial development and validation time to a product’s path to market. Switching container types also typically requires qualification and validation on a different filling line, steps that can add time and cost to key transitions in a product’s life cycle.
RTU Container Platforms: In addition to eliminating sterilization processes, many RTU container platforms also substantially increase production agility – thanks to container-agnostic configurations that enable them to process multiple different container formats.
This feature allows products to be qualified and validated on a single filling line, and then remain on that line across multiple life cycle evolutions. Additional formatting and retooling steps are typically required to switch container type, and a significantly larger logistics area is usually needed to manage tubs and trays. But the cost of these requirements often compares favorably with migrating between high-speed bulk filling lines.
Due to their uniform, standardized container inputs, RTU container platforms can also be readily automated. Automating lines that process pre-sterilized containers can help minimize risks such as manual handling, container damage, and throughput disruptions.
Of course, these risks are ones that an expert CDMO can typically manage and mitigate with any selected filling line. Nonetheless, RTU container platforms remain a valuable option for drug developers who want to reduce development timelines, de-risk filling processes by design, and transition between container formats as efficiently as possible.
CONTINUING EVOLUTION: UNLOCKING THE FULL VALUE OF RTU CONTAINER SYSTEMS
Given the many advantages of RTU container platforms, it’s likely that adoption of these technologies will continue to accelerate in the coming years. But while today’s RTU-based filling lines already deliver substantial benefits – for drug developers and manufacturers alike – there are still several key considerations the industry will need to address to unlock the full value of RTU container platforms:
Inconsistent Outer Packaging: To enable automation and minimize manual handling, RTU container platforms require consistent, harmonized inputs that can be processed with minimal variation and unpredictability. Many suppliers are already supporting this need by adopting a uniform size for the tubs and trays in which pre-sterilized containers are delivered to aseptic manufacturers.
But at the same time, the outer packaging around those tubs and trays can often vary from supplier to supplier – and sometimes within lots from the same source. This variability is common with double-bagged configurations: tubs and trays with inconsistent exterior packaging can easily disrupt automated de-bagging processes, leading to costly delays and resets. This variability must be addressed and mitigated for RTU container platforms to consistently deliver on their full promise.
Environmental Impact: While pre-sterilized containers may offer many advantages, producing and using them does come with an added ecological cost. These containers are produced and processed using energy-intensive sterilization processes, and in configurations that generate a substantial amount of waste not associated with bulk container platforms – including a variety of tubs, trays, lids, and exterior bags.
Today, these components are typically non-recyclable and must be discarded. To support our industry’s important sustainability goals, further research is required into potential solutions to the environmental challenges associated with adopting these more waste-intensive systems.
Supply Chain Limitations: Compared with filling lines that process bulk containers, RTU container platforms have substantially more exact and inflexible requirements for all container inputs. While most bulk container platforms can readily accommodate variations of the same container format, RTU container platforms can be much more sensitive to variability. They are typically configured to process vials, syringes, and cartridges that meet exact and unvarying specifications.
While uniform, standardized inputs can facilitate automation, this requirement can also add some latent risk to a product’s supply chain. In the event of a disruption or backorder, it can be challenging for an aseptic manufacturer to identify an alternative supplier with containers that meet the same exacting specifications. Further harmonization of container formats will hopefully mitigate this challenge as the industry’s adoption of RTU approaches accelerates.
While these are important considerations for today’s sterile injectable stakeholders, collaboration and innovation will no doubt address each one in future evolutions of today’s RTU container platforms. Mitigating these challenges will further enhance the impact of aseptic filling technologies that already make substantial contributions to the sterile injectable value chain – and further enhance our industry’s ability to bring new drug products to market as efficiently and sustainably as possible.
LOOKING AHEAD: PURSUING THE FULL POTENTIAL OF RTU CONTAINER PLATFORMS
Holistically considered, RTU container platforms offer numerous advantages that are important to evaluate when developing an aseptic filling process – and that will give these technologies a robust and valuable role to play in the future of aseptic filling. We expect these technologies to soon become part of the manufacturing mix for many more injectable therapies, from niche indications to high-volume commodities.
At Vetter, we’re already well-prepared to harness this trend, with ongoing investment in a range of RTU-specialized resources and infrastructure. At the same time, we’re also pursuing the kind of strategic, forward-thinking sustainability strategies that our industry will need to address the environmental impact of RTU container platforms. With the right sustainability, regulatory, and standardization solutions in place, we’re confident that these technologies can help our customers achieve the efficiency, sustainability, and quality we all hope to see in the biopharmaceutical value chain.
REFERENCE
- https://reports.valuates.com/market-reports/QYRE-Auto-2O15273/global-ready-to-use-rtu-packaging-for-pharmaceuticals.
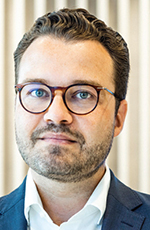
Gregor Deutschle is Director Product and Service Management. Since 2021, he has been responsible for the Product & Service management at Vetter. With his team, he takes care of matching the offerings of Vetter with the market demand and further advancing the business portfolio. This involves identifying market trends early on and verifying their potential impact on customer requirements, new products, and service needs. Prior to joining Vetter, he has worked in several roles from in-house consulting, project management, lean management, and business development. He has been working in the pharmaceutical industry for the last 12 years and started his career with a degree in Mechanical Engineering from RWTH Aachen University in 2008.
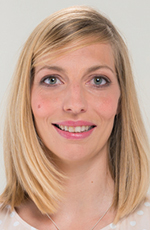
Gabriele Maier is Director/Production Site Manager at Vetter. She joined the company in 2006 after graduating with a degree in Food Science and Technology from the University of Hohenheim. She started in the department of Quality Operation and after 5 years, she switched to production and became a Production Manager at the Vetter Langenargen aseptic production plant where she gained experience with various products and bulk formats. In 2019, she was promoted to Site Manager. Then in 2021, she took over her current position of Director/Site Manager of the Vetter production site in Ravensburg South at which bulk and pre-sterilized systems are used in commercial production.
Total Page Views: 5615