Issue:June 2022
AUTOINJECTOR TECHNOLOGY - De-risking Biosimilar Development With a Clinically Validated & Commercially Proven Disposable Autoinjector
INTRODUCTION
As biosimilar development continues to accelerate with nearly $112 billion in biologic medicines set to lose exclusivity in the global market by 2025, the market is becoming increasingly competitive, putting first-to-market biopharmaceutical companies at a key advantage.1 With current timelines for biosimilar development and review from health authorities estimated to be nearly 7 years at a cost of between $100 and $300 million to develop, delays during combination product development and regulatory approvals can impact launch timelines and potential market penetration.2,3 A fundamental area in which biopharmaceutical companies can de-risk the launch process is by choosing a suitable autoinjector technology and partner.
Anticipating and retiring inherent risks in biosimilar development is one of the most essential tasks to be undertaken by companies seeking coveted first-mover status. And yet, the development and commercialization of biologic combination products to treat chronic conditions entails highly complex and challenging processes. Stringent performance requirements, together with increasing regulatory demands and intense competition, contribute to the complexity. Certain factors will be essential in establishing and maintaining an early lead. These include evaluation and selection of suitable combination product technology, and the selection of a combination product development partner with proven commercial solutions, complementary capabilities, and the expertise to positively address those complexities. A solution and partner that can help biopharmaceutical companies manage costs will be essential to achieve commercial success in a market that will only become more competitive. For many biopharmaceutical customers, BD and the BD Physioject™ Disposable Autoinjector have offered the appropriate combination of technology, documentation, and resources required for timely success.4
FACTORING IN A RAPID LAUNCH
What factors are evaluated to ensure a fast biosimilar launch? Various internal market research studies undertaken by BD suggest the chosen autoinjector should be a commercially available device that works in conjunction with a commercially available prefillable syringe.5,6 To limit the possibility of bottlenecks during assembly and production, the device should incorporate a simple design, which aims to limit the steps required for assembly to help streamline the production process. Ensuring that development support is available from the device partner is key. This should include assembly guidance documents as well as compliant documentation for regulatory approval. The ability of the device partner to provide fast access to small quantities of product during the development phase will also help support time to market. The device partner should be able to provide flexible support, including services such as combination product testing, and medical affairs and regulatory support, as required. Additional factors can include providing product customization options and the ability to meet the customers’ cost requirements.
BD PHYSIOJECT™ DISPOSABLE AUTOINJECTOR: ITS MILESTONES CAN STREAMLINE YOUR PATH TO MARKET
With an established track record of delivering medications for more than 10 years, the BD Physioject Disposable Autoinjector has attained some significant milestones. To date, more than 118 million BD Physioject Disposable Autoinjectors have been sold.7 What’s more, when integrated with the BD Hypak™ Glass Prefillable Syringe for Biotech, the BD Physioject Disposable Autoinjector has proven to be a dependable system, with greater than 99.999% reliability linked to system integration.8 Today, millions of patients and more than 15 pharmaceutical companies benefit from the robust design and manufacturing quality of the BD Physioject Disposable Autoinjector for more than 10 chronic therapeutic indications.
INTEGRATION: ONE-STOP ACCOUNTABILITY FOR PERFORMANCE OF THE TOTAL DELIVERY SYSTEM
A well-integrated system can help mitigate system performance risks early in the combination product development process. The BD approach to integration is behind the success of the BD Physioject Disposable Autoinjector system.* BD ensures components work together, helping avoid integration issues between the drug, the primary container, and the secondary solution, which can delay launch times significantly. The BD approach to integration focuses on ensuring every system component, including the barrel, stopper, needle, needle shield, primary container, and secondary delivery system, is compatible and functions cohesively. This strategy helps to develop a robust delivery system that performs as designed and meets regulatory requirements for safety, effectiveness, functionality, performance, and usability. The hardiness of this approach has proven itself over the course of 118 million autoinjectors sold for chronic applications. The BD approach to integration also means that you will have a single partner that can deliver all components of a drug delivery system, along with system-level documentation and supporting data which, in turn, create a more readily adoptable format for the critical step of combination product regulatory approval.
HUMAN FACTORS STUDIES & RECOGNIZED EASE OF USE
Biosimilars intended for self-injection must demonstrate high levels of patient safety and ease of use while working within the competitive and price pressures specific to the biosimilars market. In its more than 100 years of developing medical technologies to address healthcare challenges, BD has established a patient-centric culture reflected throughout its product design approach. BD conducts human factors engineering testing on its most advanced products across a range of representative users to confirm the integrated devices are safe for use as a system. While biopharmaceutical companies will conduct their own human factors testing with the actual formulation and intended patient population, by leveraging human factors studies in the iterative design of the BD Physioject Disposable Autoinjector, BD provides assurance in the usability of the combined components and reduces the risk of unforeseen issues.
To inform and validate the design of the BD Physioject Disposable Autoinjector, BD conducted nine human factors studies, including seven formative and two summative studies,^^ involving more than 600 individuals.9-11 In these studies, BD examined all aspects of performance, safety, efficiency patient acceptance, and ease of use, including pain perception compared with the use of stand-alone prefilled syringes.9‡ This work generated essential insights regarding the overall user-product interface and demonstrated patients’ positive response and acceptability of both the product design and the user experience.
This emphasis on human factors led to a patient-centric design and the incorporation of a robust integrated passive sharps injury protection feature. In human factors and clinical studies with over 1,300 simulated injections, the needle covering system integrated in the BD Physioject Disposable Autoinjector automatically deployed and locked in 100% of cases. 9,10^∞ The BD Physioject Disposable Autoinjector also incorporates a patient-centric design that allows the patient to control the start of the injection once the autoinjector is placed on the skin and the cap is removed. In a human factors study, 90.8% of patients with rheumatoid arthritis found that the force required to press the button was acceptable and 81.5% of patients found that the three-step injection process with the BD Physioject Disposable Autoinjector was simple.10 §¶
Specific design features include:
- Demonstrated patient usability and ease of use, especially in patients with limited dexterity eg, patients with rheumatoid arthritis10,12
- A 360° view of the drug and injection process, allowing 100% drug visibility
- A simple, one-touch injection button for activation10
- A hidden needle before and during injection, which aims to help reduce needle-stick anxiety13-15
- A protected needle before and after injection, which aims to help limit the risk of needle stick injury13-15
- A cap designed to prevent re-capping once the device has been opened13
- Two subassembly components, which aim to limit the steps required for assembly13
The patient-centric design of the BD Physioject Disposable Autoinjector was recognized in 2015 with the Ease of Use Award from the Arthritis Foundation.16
DOCUMENTATION
BD Physioject Disposable Autoinjector comes with full, supportive data packages of system performance to help de-risk development and support time to market. Documentation and support provided with the BD Physioject Disposable Autoinjector include:
- Customer product specifications
- Customer drawings
- BD Design Verification Summary Report and test methods
- ISO10993 compliance statement
- Materials of concern and safety information
- Intended use and residual risk analysis statements
- Final assembly recommendations
- BD Physioject Disposable Autoinjector validated direction for use (DFU)#
- Human Factors Engineering summary report
- List of machine manufacturers for final assembly
- Letter or Authorization (LOA) for Master Files and technical dossier
- ISO-11608 compliance quality statement
FAST ACCESS TO SAMPLES
BD provides fast access to samples for clinical use through the BD PartnerPath™ Program to ensure flexibility in supply and support time to market. The BD PartnerPath Program is for anyone with a drug in development requiring access to low quantities of product quickly. For this reason, BD can ensure availability for a multitude of products including primary containers, plunger stoppers, plastics components, and secondary devices, within 12 weeks.
THE BD PREFILLABLE SYRINGE – AT THE HEART OF DE-RISKED SYSTEM INTEGRATION
Since 2014 more than 3.9 billion BD Glass Prefillable Syringes have been sold to support the delivery of injectable biotech drugs.17 BD Physioject Disposable Autoinjectors are fully integrated with the BD Hypak™ for Biotech Glass Prefillable Syringe and fully compatible with the BD Neopak™ Glass Prefillable Syringe.
The BD Hypak™ for Biotech Glass Prefillable Syringe is a fully integrated Prefillable Syringe and key component in the more than 10-year success and track record for reliability of the BD Physioject Disposable Autoinjector. The BD Hypak for Biotech Glass Prefillable Syringe is a commercially proven, sterile, clean and ready-to-fill (BD SCF™) syringe barrel container featuring key compatibility factors for biotech drug delivery. It offers limited reject rates on customer process through fewer visual/cosmetic defects, and improved drug compatibility through specified low tungsten residue levels.18-19† Its controlled Length Under Flange and gliding specifications are the foundation of its compatibility with the BD Physioject Disposable Autoinjector.19
The BD Neopak™ Glass Prefillable Syringe platform has been developed leveraging the expertise and experience BD has acquired during its more than 30 years of collaboration with the biopharmaceutical industry.20 The BD Neopak Glass Prefillable Syringe platform is designed to address key needs of biotech manufacturers such as drug and autoinjector compatibly.21,23 Fully compatible with the BD Physioject Disposable Autoinjector, the BD Neopak 1 mlL Glass Prefillable Syringe features increased resistance to breakage, specified low and ultra-low tungsten residual levels, and reduced silicone quantity aiming to support reliable performance.22,23††
SERVICES TAILORED TO SUPPORT YOUR COMBINATION PRODUCT DEVELOPMENT JOURNEY
To every partnership, BD offers a range of end-to-end services based on experience in designing and integrating components into systems and extensive collaboration with drug developers and biosimilar manufacturers. These services are designed to help biopharmaceutical partners choose the correct components and systems for their applications, to assess and offer solutions to any potential challenges or sensitivities, and to help produce the necessary data packages needed to demonstrate the safety and performance of the integrated combination product.
These services include the following:
- Analytical and bioanalytical chemistry capabilities
- Formulation services
- Functional and performance testing
- Clinical/human factors consultancy
- Combination product documentation support and testing
- Process consultancy
- Regulatory support
Combination product support occurs throughout the development process, from matching the right set of components with the formulation in Phases 1 and 2, to validation testing of the system in Phases 2 and 3. BD offers this breadth of capabilities in combination with the entire system of components to enable customers to anticipate and resolve challenges before they become issues from a system performance perspective.
SUMMARY
Depth of in-market experience with primary containers and secondary solutions, confirmed rigor in product development processes informed by more than 30 years of expertise in injection science and translational research, and an extensive global manufacturing network, are advantages BD can offer as a partner. BD leverages these assets to develop innovative solutions that provide peace of mind for customers and contribute to patient well-being, and de-risked combination product development and commercialization. For these reasons, the BD Physioject Disposable Autoinjector has been chosen by biopharmaceutical customers developing new biologics or biosimilars in 1mL applications.
*When integrated with BD Hypak™ for Biotech Glass Prefillable Syringe
†As compared to BD Hypak Prefillables Glass Syringes
††As compared to BD Hypak™ for Biotech Glass Prefillable Syringe
**A number of services can be provided at an additional cost
‡In a clinical study with 40 healthy volunteers, at the end of the last session, subjects were told they will have an unscheduled additional injection. The results showed that all 40 subjects (100%) preferred the BD Physioject™ Disposable Autoinjector for that injection (which was not done, the question was solely for informational purposes).
^In a human factors study with 65 patients with rheumatoid arthritis, 100% (n=390/390 injections) of passive sharp injury prevention feature activation was recorded.
∞ In a clinical study with 40 healthy volunteers, the passive sharp injury prevention feature activation was recorded 100% (n=480/480 injections) of the time.
* In a human factors study with 65 patients with rheumatoid arthritis, after 6 simulated injections, n=59/65 (90.8%) of patients with rheumatoid arthritis gave a score ≥6 on a 0-10 Likert scale for acceptance of further self-injections with BD Physioject™ Disposable Autoinjector.
¶ In a human factors study with 65 patients with rheumatoid arthritis, after 6 simulated injections, the mean acceptance for the 3-step injection process (perceived required force to press the button, force to maintain the device on skin and perceived visibility of the move of the stopper during the injection) was 81.5% where patients with rheumatoid arthritis gave a score ≥6 on a 0-10 Likert scale.
# Directions for Use (DFU) are provided to support development of the instructions for use (IFU)
^^Between 2005 and 2010, BD conducted 7 formative and 2 summative studies, involving over 600 individuals.
REFERENCES
- IQVIA Institute – Spotlight on Biosimilars, June 2021.
- McKinsey & Company, “An inflection point for biosimilars”, 2020, https://www.mckinsey.com/industries/life-sciences/our-insights/an-inflection-point-for-biosimilars, consulted online January 19, 2022.
- Bossart, J. (2020), “DEVELOPMENT TIMELINES – Drug Development Times, What it Takes – Part 2”, Drug Development & Delivery, https://drug-dev.com/development-timelines-drug-development-times-what-it-takes-part-2/.
- BD Physioject™ Disposable Autoinjector launched with commercialized drugs.
- BD Sutton’s Creek Qualitative Market Research [internal study],Franklin Lakes NJ; Becton, Dickinson and Company; 2021.
- BD Autoinjector Market Research Preliminary Report, 2022.
- BD WW Demand Database, 2012-2021.
- BD Quality System complaint data – Complaint extract for reported user complaints related to system integration.
- Berteau et al. (2010), “Evaluation of performance, safety, subject acceptance, and compliance of a disposable autoinjector for subcutaneous injections in healthy volunteers.” Patient Preference and Adherence, Vol. 4, p. 379-388.
- Schwarzenbach et al. (2014), “Results of a human factors experiment of the usability and patient acceptance of a new autoinjector in patients with rheumatoid arthritis,” Patient Preference and Adherence, Vol. 8, p. 199-209.
- Summary Report – BD Physioject Formative Evaluations (CHFIN 21-31).
- Physioject™ Human Factors Engineering Report [internal report], Le Pont-de-Claix, France; Becton, Dickinson and company; 2021.
- Physioject™ design input specification [internal report], Le Pont-de-Claix, France; Becton, Dickinson and company; 2014.
- Physioject™ design verification report [internal report], Le Pont-de-Claix, France; Becton, Dickinson and company; 2014.
- Physioject™ external R&D document. BD Physioject™ ISO23908:2011 Assessment of Compliance [external report], Le Pont-de-Claix, France; Becton, Dickinson and company; 2021.
- Fain W.B, and Mann E., “BD Physioject Disposable Autoinjector Evaluation Report of Consumer Product Accessibility for Users with Arthritis”, Georgia Tech Research Institute, Georgia Institute of Technology, April 2015.
- Internal analysis, BD internal sales (Vendavo Extract FY14 FY21).
- Validation Summary Low Tungsten BD Hypak™ for Biotech Prefillable Syringe Barrels [Internal Study], Le Pont-de-Claix, France; Becton, Dickinson and Company; 2012.
- BD Hypak™ for Biotech customer quality specification, Le Pont-de-Claix, France; Becton, Dickinson, 2017.
- BD Medical Pharmaceutical Systems, BD Hypak™ Glass Prefillable Syringe since 1975_BD Website.
- BD Neopak™ 1mlL customer quality specification, Le Pont-de-Claix, France; Becton, Dickinson and Company; 2017.
- BD Neopak™ 1mlL design input specification [internal study], Le Pont-de-Claix, France; Becton, Dickinson, 2010.
- Traction bench test and visual inspection results: BD Neopak™ vs BD Hypak™ for Biotech improved specifications [internal study], Le Pont-de-Claix, France; Becton, Dickinson and Company; 2018.
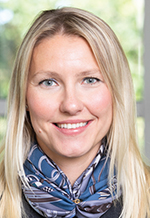
Victoria Meyer has worked at BD for more than 14 years across several business units in various commercial roles, including sales, sales operations, and regional marketing. She is currently the Senior Global Strategic Marketing Manager responsible for leading 1 mL product platforms across the BD Biologics Portfolio. In this role, she closely partners with Research & Development and other cross functional teams to define, develop, and deliver programs, data sets, and system solutions to pharmaceutical customers to help support combination product development. She earned her MBA from Columbia Business School and her undergraduate degree in Economics from the College of the Holy Cross.
Total Page Views: 7303