Issue:October 2022
TOP SPRAY GRANULATION - POLYOX™: Producing Lightweight Metformin Hydrochloride Extended-Release Tablets for Patient Adherence & Cost-Effective Manufacturing
INTRODUCTION
In recent years, drug development has been trending toward reducing tablet weight while maintaining similar drug performance to improve patient adherence. Reducing tablet weight is especially prevalent in the formulation of Metformin Hydrochloride extended-release tablets, which are widely used in long-term Type II diabetes treatment. While Metformin Hydrochloride tends to be efficaciously delivered via extended-release tablets, this delivery format usually leads to larger tablets that are difficult to swallow, thereby increasing the risk of reduced patient compliance.1
Patient noncompliance contributes to 50% of all treatment failures and adds billions of dollars to healthcare costs worldwide.2 Smaller, lighter tablets with better drug delivery design have the power to solve this problem and boost patient adherence. However, formulating smaller extended-release tablets can be challenging, expensive, and time-consuming. Often, drug developers struggle with controlling the drug release of a smaller tablet at a definite rate. Understanding the challenges associated with developing smaller extended-release tablets, and the excipient-based solutions to these challenges, will empower formulators to develop robust, stable drug formulations with high patient adherence while cutting manufacturing costs.
THE STUDY
Today, commercially available Metformin Hydrochloride extended-release tablet formulations are generally based on matrix technology or osmotic controlled-release technology. Drug manufacturers can simplify the production of these extended-release tablets by using top-spray granulation processes.
While POLYOX™ — an excipient with a granular or spherical morphology — is generally used during high-shear granulation techniques, this study explores the development of POLYOX-based Metformin Hydrochloride extended-release tablet formulation via top-spray granulation to achieve ease of dosing and cost-effective manufacturing. During the study, IFF Pharma Solutions investigated the development of metformin hydrochloride extended-release tablets (500 mg) by top-spray granulation processes and the compaction properties of the developed granules.
BACKGROUND
Various aspects of granulation — such as optimal addition rate of binder solution, impeller and chopper speed, wet-massing time, and milling of dried granules — impact the manufacturing process and should be studied carefully for successful development.3 High-shear granulation increases manufacturing steps, time, and cost, while top-spray granulation provides the advantage of simultaneous granulation and drying in the same equipment, making it a great choice for continuous manufacturing.
Pharmaceutical manufacturers should remain aware of some of the potential challenges of the top spray granulation process. Excessive temperature or moisture could cause agglomeration of POLYOX, leading to particles sticking to the fluid bed processor’s (FBP) internal surfaces, including the base plate. Air blockage may cause uneven temperatures and air distribution, which can lead to an agglomeration of particles and an unfeasible batch.
In this investigation, low tablet weight POLYOX-based Metformin Hydrochloride extended-release tablets were developed, and the compaction properties of the granules were evaluated.
MATERIALS
POLYOX water-soluble polymers for pharmaceutical applications possess a unique set of properties that allow for distinctive drug delivery solutions. They exhibit many properties typical of other classes of water-soluble polymers, including lubricity, binding, water retention, thickening, and film formation. Supplied in a wide range of molecular weights to meet specific formulation and processing requirements, the advantages of POLYOX include fast hydration, rapid swelling, thermoplastic properties, superior adherence, and more.
They are free-flowing hydrophilic powders supplied in a variety of viscosity grades corresponding to approximate molecular weight, ranging from 100,000 to 7,000,000 Daltons; this versatility has made POLYOX a popular choice for many pharmaceutical applications, especially when it comes to managing tablet weight. Typically, used as an excipient in controlled-release formulations, POLYOX can also provide a robust matrix-based system when formulating smaller tablet weights and sizes via top-spray granulation.
Materials used in development include Metformin Hydrochloride, and various grades of POLYOX WSR polymers, Hypromellose (METHOCEL™ E5 Premium LV), and Magnesium stearate.
METHODS
Development of Metformin Hydrochloride Extended-Release Tablets (500 mg)
To prepare lightweight Metformin Hydrochloride extended-release tablets for the dissolution study, researchers sifted Metformin Hydrochloride and POLYOX WSR Coagulant through No. 20 mesh and loaded them in GPCG 1.1 top-spray bowl. The blend was granulated using METHOCEL E5 Premium LV dissolved in purified water. The process parameters for FBP top-spray granulation monitored include product temperature in the range of 30°C to 40°C, spray rate 3 to 7 g/min, and drive speed in the range of 20 to 40 m3/h.
The granules were then blended with lubricant magnesium stearate using a double cone blender (Bowman Archer Ltd), and tablets containing 670 mg of granules were compressed using a circular 12-mm punch on a single rotary compression machine (Kambert Engg. Pvt Ltd). Compressed tablets were then evaluated for physical attributes like hardness and thickness.
For the dissolution of Metformin Hydrochloride extended-release tablets (500 mg), researchers carried out in vitro studies to optimize the formulation and evaluate the performance of the finished product. For dissolution, test, and specification listed in Metformin Hydrochloride extended-release tablets monograph of USP pharmacopeia was followed.4 The Dissolution condition consists of 900 ml of 6.8 pH phosphate buffer media in USP type I apparatus (basket method) at 100 rpm.
Researchers evaluated the stability performance of the POLYOX-based Metformin Hydrochloride extended-release tablets (500 mg). Tablets were packed in a triple laminated pouch and charged on stability condition at 40°C/75% RH (stability chamber by Neutronics equipment company Ltd.). Dissolution was performed at different time intervals (1, 3, and 6 months) and was compared with the initial release data.
Compaction Study
The compaction properties of different grades of POLYOX and POLYOX-based Metformin Hydrochloride extended-release granules were studied using a compaction simulator (ESH compaction simulator, UK). The tablet compression was carried out with a 13-mm flat, D-type tooling punch, and the physical evaluation of the compressed tablets (viz, hardness, thickness, and diameter) was performed after 24 hours of storage at ambient temperature and controlled humidity. Researchers calculated the tensile strength for each tablet from obtained hardness, thickness, and diameter of the tablet, then plotted it against the compression pressure.
RESULTS & DISCUSSION
Development of Metformin Hydrochloride Extended-Release Tablets (500 mg)
The composition was optimized and screened for the quantity of controlled release polymer (POLYOX WSR Coagulant) to obtain the desired release profile at 3 hours (Table 1).
The dissolution study showed that, as the concentration of the POLYOX WSR Coagulant increased, the drug release was decreased at 3-hour intervals. F3 formulation showed the desired drug release, therefore the same was used for further studies. The top-spray granulation process was satisfactory and did not show any processing challenges like agglomeration and uneven distribution of the binder. Physical properties observed for the granules (F3) are shown in Table 2.
Flow property data showed the poor flow of the granules. Particle size distribution of the granules (Table 3) suggested increased fine proportion as compared to the granular portion. This can be attributed to a higher proportion of the API (Metformin Hydrochloride) present in the composition (~75% w/w).
Lubricated granules were subjected to compression using round shape punches. The compression process was found satisfactory, and the finished product did not show any tablet defects – physical parameters were observed for the compression process.
The results reflected white to off-white round tablets with an average weight of 670 mg. The diameter of the tablet was 12 mm, and the thickness was reported to be 6.10 to 6.20 mm. Researchers found the hardness to be about 5 to 6 kP.
Researchers carried out the dissolution study as per Metformin Hydrochloride extended-release tablets monograph in USP. This clearly represents that the prototype with low-tablet weight complies with USP dissolution specification (3 hours-20% to 40%, 3 hours-45 % to 65% and 10 hours-NLT 85%).
An accelerated stability study (40°C/75% RH) showed consistent dissolution of the developed formulation over the study period (6 months), proving the stability of Metformin Hydrochloride extended-release tablets. In addition, the packaging material (aluminum pouch) of the drug product during the stability study might have helped to achieve the consistent drug release across the stability period.
Compaction Study
Researchers calculated the tensile strength for each tablet from obtained hardness, thickness, and diameter of the tablet, then plotted it against the compression pressure. The Metformin Hydrochloride extended-release granules were studied for compaction profile (Figure 2). The compaction slope observed for base polymer (POLYOX WSR Coagulant) was 0.036, and for Metformin Hydrochloride extended-release granules, it was 0.051. Data suggests the formed granules had better compactability compared to the base polymer. The change in compactability can be attributed to the proportion of API (~75% w/w) in the formulation.
CONCLUSION
The primary advantage of top-spray granulation processes is ease of aqueous granulation with no rigorous milling process required because top-spray granulation provides a controlled granulation process. Fewer manufacturing steps means the process is easily adoptable to continuous manufacturing processes and leads to a cost- effective, better controlled process. The successful application of top-spray granulation led to the development of Metformin Hydrochloride extended-release tablets (500 mg) that were small and round, providing ease of dosing, as well as stable and consistent product dissolution.
Drug developers face several challenges when formulating lightweight tablets for extended release, maintaining a definite release rate being the main challenge. Low-weight tablets lead to better patient compliance, and this study demonstrated a cost-effective alternative with the same quality attributes of the finished product.
Overall, the study shows the application of POLYOX-based top-spray granulation to manufacturing smaller Metformin Hydrochloride extended-release tablets. By incorporating top-spray granulation into the manufacturing processes for extended-release tablets and formulating with patient needs in mind, formulators will equip the pharmaceutical industry with improved patient compliance and therapy outcomes, while reducing costs and increasing efficiency.
REFERENCES
- Formulation and Characterization of size reduced oral extended-release Metformin tablets, Asian Journal of Chemistry, 22 (3), 2442-2444, 2010
- J H Flory and A I Mushlin, Effect of cost and formulation on persistence and adherence to Initial Metformin Therapy for type 2 diabetes, Diabetes Care, 43, e66- e67, 2020.
- Manish Rane, Application of Polyethylene oxide in Hydrophilic Matrix Tablets, Pharma Times 45 (3) 41-48, 2013.
- Metformin Hydrochloride Extended-Release Tablets, USP Pharmacopoeia, 2010.
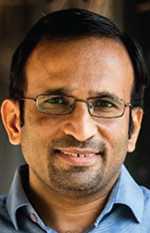
Dr. Atul Lohade is the Senior Application Specialist in Pharma Solution Business at IFF. He earned his PhD (Tech) in Pharmaceutics from the University of Mumbai. His expertise and focus are in solid oral, liquid oral, and topical-based drug delivery technologies.
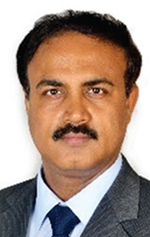
Dr. Tejas Gunjikar is the Pharma Application and Innovation Leader at IFF, focused on drug delivery technologies, biopharmaceutical formulations, solid oral dosage forms, and more. He earned his PhD in Pharmaceutics from University of Mumbai, and his Bachelor’s degree in Pharmacy from Savitribai Phule Pune University.
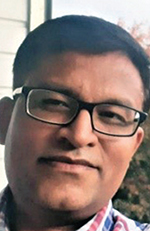
Vinay Muley is an R&D lead at IFFAC (IFF Application Center), Hyderabad, India, managing a group of scientists working in pharmaceutical excipient science.
Total Page Views: 4410