Issue:March 2021
FORMULATION FORUM - Considerations in Development & Manufacturing of Complex Injectables for Early Phase Studies
BACKGROUND
A complex injectable is a product that has a complex active ingredient, complex formulation, complex route of delivery, or complex drug device combinations. Complex parenteral products include delivery systems, such as sterile suspensions, liposomes, lipid nanoparticles, emulsions, polymeric microspheres, pellet implants, etc, for administration of drug via the injection, ophthalmic, subcutaneous, implant route, etc. Complex injectables have gained increasing attention due to their advantage in applications in both acute and chronic diseases treatments. Particularly, suspensions and lipid-based nanoparticles are being increasingly utilized due to their ability to increase drug loading to improve bioavailability/stability and to enable long-acting injectable of poorly soluble drugs and biologicals.
However, the development and manufacturing of those injectables is extremely complex, requiring careful design of formulation and process, in-depth characterization of products, confirmation of safety and efficacy per FDA regulation, and high-quality standards in manufacturing, packaging, distribution, and storage.
Production of the first clinical trial materials for a new pharmaceutical dosage form is a significant milestone event in the development of a pharmaceutical product. As a product transitions from pre-clinical development to the clinical development phase, the manufacturing process takes on a much greater role in the overall success of the project. This transition is particularly difficult for emerging pharmaceutical companies whose expertise typically lies in the biology and chemistry, and less on the engineering, regulatory, and quality aspects of manufacturing the drug product. This critical milestone is made even more challenging when the drug product is intended to be a sterile injectable dosage form.
COMPLEX INJECTABLE DOSAGE FORM DEVELOPMENT
Suspensions/Nanosuspensions
The primary consideration for suspensions is physical stability, ie, they tend to settle over time and to change in particle size distribution. Physical stability in suspensions can be controlled by (1) the addition of flocculating agents to enhance particle “dispersability,” (2) the addition of viscosity enhancers to reduce the sedimentation rate in the flocculated suspension; and (3) selection of appropriate stabilizer and surfactant. The addition of the flocculating agent, at some critical concentration, negates the surface charge on the suspended particles and allows the formation of floccules, or clusters of particles, that are held loosely together by weak van der Waals forces. Because the particles are linked together only loosely, they will not cake and may be easily re-dispersed by shaking the suspension. Viscosity enhancers are typically hydrocolloids (natural, semisynthetic, or synthetic) used in a concentration that overcomes the suspended particle’s tendency to settle.
A couple of methods have been used to prepare parenteral suspensions. First, aseptically combining sterile powder and vehicle involves aseptically dispersing the sterile, milled active ingredient(s) into a sterile vehicle system; aseptically milling the resulting suspension as required, and aseptically filling the milled suspension into suitable containers. Second, in-situ crystal formation by combining sterile solutions. In this method, active ingredient(s) are solubilized in a suitable solvent system, a sterile vehicle system or counter solvent is added that causes the active ingredient to crystallize, the organic solvent is aseptically removed, the resulting suspension is aseptically milled as necessary, and then filled into suitable containers. Sterility of those suspensions can be achieved by an aseptic process or by a terminal sterilization if those suspensions have enough thermal or irradiation stability upon the sterilization process.
Lipid-Based Nanoparticles
Lipid-based nanoparticles, such as lipid complexes, lipid nanoparticles, and liposomes, are formed from lipids and other excipients in aqueous medium. Lipid nanoparticles can be produced by dispersion of lipids in water via mechanic energy, such as high-pressure homogenization or microfluidics. This results in the formation of lipid nanoparticles. Further extrusion may be utilized to refine the particle size distribution to a narrower range. Lipid nanoparticles can entrap both hydrophilic and hydrophobic drugs, and drug release can be targeted to specific sites. Typically, the particle sizes of lipid nanoparticles range from 50 to 200 nm. To make lipid nanoparticles suitable for therapeutic applications, their size distribution has to be controlled, which can be realized via mechanic energy or by extrusion membranes with defined pore size. In order for lipid nanoparticles to be processed by 0.22-micron sterile filtration, its particle size distribution has to be well below 200 nm; otherwise, an aseptic process needs to be utilized.
Emulsions/Microemulsions
Emulsions can be characterized as macroemulsions, microemulsions, or nanoemulsions. Macroemulsions are typically opaque in appearance because the average particle size of the hydrophobic droplet in a macroemulsion is typically > 500 nm and thus scatters light. Microemulsions and nanoemulsions are obtained when the size of the droplet is typically in the range of <500 nm. The distinction between microemulsions and nanoemulsions relates to their thermodynamic stability. Microemulsions are thermodynamically stable due to the use of sufficient co-solvents and co-surfactants to prevent Ostwald ripening. Nanoemulsions contain much less of the stabilizing co-solvents and co-surfactants, and as such, are meta-stable and more susceptible to Ostwald ripening.
The emulsion can be prepared via high-energy and low-energy methods. A high-energy method includes high-pressure homogenization, micro-fluidization, and ultrasonication normally used to make emulsions; whereas low-energy methods, including the phase inversion emulsification method and the self-emulsification method, are utilized to prepare microemulsions. Terminal sterilization will be used if the emulsion has good thermal stability, otherwise aseptic process or filter sterilization will have to be exploited. In order to enable 0.22-micron sterile filtration, the emulsion’s particles size distribution needs to be below 200 nm, and its viscosity should be low enough for formulation to flow freely through the filtration membrane.
Polymeric Nano/Microparticles
To realize long-acting attributes, the polymeric macro/nanoparticles can protect the drug from burst release and degradation, thus achieving prolonged drug delivery and a longer shelf-life. For therapeutic purposes, the most commonly used polymers include polyethylene glycol (PEG), poly(lactic acid) (PLA), poly(lactic-co-glycolic acid) (PLGA), poly(ε-caprolactone) (PCL), alginate, chitosan, and gelatin base. Polymeric microspheres can be developed based on hydrophobic materials that facilitate controlled release of the therapeutic. This is achieved via slow degradation of the microsphere’s polymer backbone that subsequently leads to kinetically driven release of the drug. Long-established polymer microspheres that have had significant success are based on incorporation of leuprolide (a testosterone-inhibiting drug) into polylactide (PLA) and polylactide-co-glycolic acid (PLGA) microspheres. Sterility of polymeric microparticles can be achieved via aseptic process or by terminal sterilization if the product has enough thermal or irradiation stability upon the sterilization process.
GMP CONSIDERATIONS OF COMPLEX INJECTABLES
Regulatory Requirements
On September 15, 2008, the FDA made effective an amended rule that applies to small molecule drugs and biologics, including vaccines and gene therapy products. The note in the Federal Register of July 15, 2008 (Volume 73, No. 136) announced an adaptation of 21 CFR 210 and 211: investigational medicinal products solely intended for use in Phase 1 are to be exempted from complying with the “final rule” under FD&C Act 505(i) (21 U.S.C 355(i)). The text stresses that the cGMP requirements of 21 CFR 211 are applicable only to Phase 2 and Phase 3 drugs. This makes a solid rationale for Phase 1 clinical trials production to focus on safety of manufacture rather than qualification of processes at this point of drug development.
In addition to product quality, sterility and non-pyrogenicity are of utmost importance for Phase 1 sterile manufacture. The injectable product can be terminally sterilized in its packaging or manufactured aseptically. Aseptic manufacturing of sterile products is still seen as a last resort that is only acceptable if all methods of terminal sterilization in the final sealed container fail. In the US, the FDA’s 2004 publication Guidance for Industry Sterile Drug Products Produced by Aseptic Processing describes the expectations of the FDA for the validation of aseptic processing in a more detailed manner. This guidance updates the 1987 guidance primarily with respect to personnel qualification, cleanroom design and isolators, air supply system, integrity of container closure systems, process design, quality control, environmental monitoring, and review of production records.
Facility, Environment & Equipment
In early phase trials, the quantity of the drug substance available is often very small. Matching the equipment scale and material handling expertise with the product batch size is essential in order to ensure a successful, cost-effective outcome. Fill and finish CMOs that manufacture high-volume commercial products typically lack the equipment and personnel to manage a developing product that requires low volume and flexibility in scheduling. Companies that specialize in small-volume early stage products have staff experience in rapid small-scale manufacturing campaigns. A smaller support staff generally has greater flexibility with regard to changes and timing. The lead time for changes at a smaller CDMO should be less than larger CMOs. Although larger CMOs have much greater capacity, they tend to be more rigid and generally have defined systems in place that are not easily changed and longer lead time.
The environment in which the aseptic processing takes place may require use of class 100 clean room suites, laminar flow hoods, biosafety cabinets, isolators, and restricted access barrier system (RABS). It is important to have suitable air flow during compounding and manufacturing. All of the air delivered to a cleanroom should pass through HEPA filters. The aseptic process should also include environmental monitoring to ensure microbiological control over the product.
The equipment used for the sterilization needs to be monitored with calibrated temperature probes and sterilization cycles that are documented and incorporated into the batch record. The product’s contact surface of manufacturing equipment needs cleaning verification following production. Items that cannot be sterilized must be disinfected before brough into the cleanrooms, and the entire area should be disinfected after processing.
Production Process & Validation
The production process should ensure the sterility and low endotoxin level of the product. If filtration is used as a method of sterilization, filters are bubble point tested to ensure integrity. To achieve the aim of a sterile product by an aseptic process, several aspects have to be considered and processes validated. In the end, process simulation with media fill is the key validation measure and allows the final evaluation of the appropriateness of the entire process. Process validation includes checks on the process by means of process simulation tests using microbial growth media (ie, media fill tests). The validation covers filling of media, environmental monitoring, and incubation and evaluation of the filled vials. Microbial control is critical as a part of cGMP for sterile products. Proper aseptic technique, properly functioning equipment, and adequate cleaning processes are to be demonstrated using media fills. Media fills are conducted routinely in order to establish that the process, environment, and controls are capable of producing a sterile drug product via an aseptic process.
Quality Control
The Quality Control department is responsible for the release of the finished drug product per specification and review of the manufacturing batch record to ensure that procedures are followed, investigations are performed if any, any subsequent corrective actions are incorporated, and that all testing performed during the process meets specifications so that the product is demonstrated to be sterile and meet product quality attributes. Micro testing for the finished product includes sterility testing per USP <71>, endotoxin testing per USP <85>, and bioburden testing per USP <61>.
Laboratory Controls
Laboratory tests used in manufacturing (eg, testing of materials, in-process material, packaging, drug product) should be scientifically sound (eg, specific, sensitive, and accurate), suitable and reliable for the specified purpose. The main purpose of laboratory testing of a Phase 1 investigational drug is to evaluate quality attributes, including identity, strength, potency, and purity, etc. The extent of analytical procedures and methods validation necessary will vary with the phase of the IND. The main goal of performing “staged” validation in early drug development is to provide test procedures that are reliable, able to support clinical studies, and evaluate the safety of the product.
Calibration and maintenance of laboratory equipment at appropriate intervals according to established written procedures is required. Personnel verify that the equipment is in good working condition when samples are analyzed (eg, system suitability). Initiation of a stability study using representative samples of the Phase 1 investigational drug to monitor the stability and quality of the Phase 1 investigational drug during the clinical trial (ie, date of manufacture through date of last administration) should be performed under ICH temperature, humidity, and light storage conditions.
Personnel & Training
All personnel involved in the manufacture of clinical trial material are to be trained in cGMP aseptic techniques. The procedures established should be clearly written and followed throughout the entire manufacturing process. Personnel are the main source of contamination of cleanrooms with microorganisms. The education and training of the personnel, the garments, the dress procedures, the rules for entry, and the behavior inside the clean rooms are important factors. Very important for aseptic manufacturing processes are the detailed SOPs of the CDMO, such as aseptic operation, gowning, room cleaning, as well as personnel and room environmental monitoring procedures.
SUMMARY
Complex injectables have gained increasing popularity in their applications in both acute and chronic disease treatments for small molecules and biologicals. However, production of the early phase clinical trial materials for complex injectables is a challenging task. A niche CDMO, which has specialized technologies in complex injectable development and adopts GMP practice with a “laboratory setting,” will have greater flexibility regarding changes, timing, and cost for successful manufacture of complex injectables in early phase development of therapeutic drugs.
To view this issue and all back issues online, please visit www.drug-dev.com.
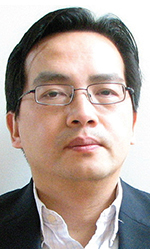
Jim Huang, PhD
Founder & CEO
Ascendia Pharmaceuticals
j.huang@ascendiapharma.com
www.ascendiapharma.com
Total Page Views: 7806