Issue:May 2020
LYOPHILIZATION - Process Monitoring During Freeze-Drying
INTRODUCTION
Freeze-drying, also known as lyophilization, is the process of removing ice from a formulation through sublimation. This typically consists of three different steps during the process. First, the solution is cooled to freeze the material. Next, primary drying is conducted to remove bulk ice by establishing a pressure differential between the vapor pressure of ice at the sublimation front and the vapor pressure of ice in the condenser. This is established through manipulation of the shelf temperature and chamber pressure to control the product temperature. The temperature of the product is increased after removing bulk ice to provide energy to remove unfrozen water during secondary drying. In-process data are needed during each step to understand the effect of shelf temperature, product temperature, and chamber pressure throughout the process. These data and other types of data provide information to ensure the product temperature remains below the failure point and provide information on when each processing step is complete. The conventional methods of process monitoring include using devices that measure temperatures and pressure within the freeze-dryer. These include, but are not limited to, thermocouples, resistance temperature detectors (RTDs), capacitance manometers, and Pirani gauges. The following describes the devices used for process monitoring and how they can be used to detect end points during the process.
INSTRUMENTS FOR MONITORING TEMPERATURE
Temperature is monitored at many different locations on the freeze-dryer and may also be used for monitoring the product. There are a few different types of sensors that are used for the equipment and the product. One type of sensor is a thermocouple that consists of two wires constructed of different metals joined at the ends (Figure 1). A voltage difference is created when the ends of the wires are placed at two different temperatures and a current flows. This is known as the Seebeck effect.1 There are different types of thermocouples that are used for different purposes (Table 1). Type T thermocouples are most often used in freeze-dryers for monitoring product temperature. Thermocouples sense temperature at the point where the wires form a junction. Therefore, they are considered point sensors. The advantage is that they are easy to use and the wires are narrow and flexible.
Another type of temperature sensor is a resistance temperature detector (RTD) (Figure 2). They typically consist of a coil of fine wire, such as platinum, copper, or nickel, wrapped around a glass or ceramic core. The resistance of the metal changes in a precise, linear way with temperature. An RTD senses temperature throughout the area of the wire. Therefore, they are considered area sensors. They are bulkier than thermocouples, but are more accurate, precise, linear, and have less drift than thermocouples. Freeze-dryers are typically equipped with RTDs for all fixed temperature measurements.
A third type of temperature sensor is the Tempris® system (Figure 3).3 It is a wireless sensor consisting of a handmade quartz crystal that oscillates in a temperature-dependent frequency. The sensor is excited by a modulated microwave signal, and the response is overlaid with the carrier signal leading to a frequency shift from which the product temperature is derived. The crystal is attached to an antenna that is threaded through the stopper. The data is transferred from the individual sensor to another antenna connected to a data recording device located outside of the lyophilizer. However, designs are available that include placing the data collection antenna inside of the lyophilizer to improve signal collection.
The Tempris sensor and RTDs are both available as wireless sensors and are amenable to steam sterilization. The wireless format allows for placement of the sensors in vials along the conveying line so they can be located in different locations across the shelf without risking sterility assurance.
Temperature sensors are necessary for monitoring product temperature at laboratory-scale. The goal is to place the sensor touching the bottom center of the vial because that is the location of the last quantity of ice before sublimation is complete. Temperature sensors are used in the laboratory to collect information on product temperature as a function of chamber pressure and shelf temperature and as a method of determining when sublimation is complete in the monitored vials. The challenge is that sensors placed in the vials may act as seeds for ice nucleation. Vials equipped with sensors exhibit less supercooling than the rest of the batch before ice nucleation and, therefore, behave differently than the rest of the vials.
Product temperature is often monitored during scale-up batches in the manufacturing area. Some manufacturing sites also monitor product temperature during routine batches. Wireless sensors are more amenable to routine use than thermocouples that must be attached to a data collection port. This restricts the use of thermocouples to vials located on the front edge of a shelf due to the connection to a port and to reduce the risk to sterility assurance. The challenges with routine monitoring of product temperature are that the monitored vials do not behave the same as the rest of the vials in the batch, and sensors may not remain in the solution in the vial or the desired location within the vial. The data received from sensors that do not remain in place are no longer valid, but still must be explained during evaluation of the in-process data.
INSTRUMENTS FOR MONITORING PRESSURE
Pressure is another in-process measurement that can be used to evaluate the progress of the cycle. Pressure within the lyophilizer is often monitored using a capacitance manometer and may also include a Pirani gauge. A capacitance manometer measures the setpoint pressure in the lyophilizer. This is possible because the output for the capacitance manometer is independent of gas phase composition. The device consists of a diaphragm that moves due to small changes in pressure and results in changes in the recorded capacitance.2
Another device used to monitor pressure is known as a thermal conductivity gauge or Pirani gauge. The gauge uses a heated filament that carries current that is surrounded by the gas being measured. The thermal conductivity changes as the pressure changes or in the case of lyophilization, as the level of water vapor changes in the product chamber. The pressure during the main portion of primary drying appears higher than detected by the capacitance manometer, indicating there is a high level of water vapor in the chamber. The pressure detected by the Pirani gauge decreases toward the end of primary drying and becomes similar to the pressure detected by the capacitance manometer. This phenomena makes comparing the differences in pressure detected by the two gages an easy method for determining the endpoint of primary drying.
The filaments within the Pirani gauges can be constructed of different metals, and some of the metals are not as amenable to repeated sterilization cycles as others. It is important to know the materials of construction for the filaments and to choose gauges equipped with platinum–rhodium filaments if they will be subjected to sterilization cycles.
METHODS OF MONITORING THE PROGRESS OF FREEZE-DRYING CYCLES
The instruments for measuring temperature and pressure during a lyophilization cycle provide data for interpretation of the progress of the cycle. The easiest method of detecting the endpoint of primary and potentially secondary drying is by comparing the pressure measured by the capacitance manometer and Pirani gauge. The pressure detected by the Pirani gauge decreases toward the end of primary drying and matches closely with the pressure detected by the capacitance manometer (Figure 4). Their convergence indicates the end of sublimation. Figure 4 also provides product temperature data measured using thermocouples. The end of sublimation in the individual vials is indicated by the steep increase in product temperature and varies depending on the location of the vial on the shelf. Note that the product temperature of the monitored vials increases approximately 10 to 20 hours sooner than convergence of the pressure data. Basing the endpoint of primary drying on the rise in product temperature detected by the monitored vials could lead to prematurely advancing the cycle to secondary drying.
Similarly, pressure rise testing can be used to detect the endpoint of primary drying. This method also compares the pressures detected by the capacitance manometer and the Pirani gauge. However, the comparison is made after closing the isolation valve located between the product chamber and the condenser and monitoring the rise in pressure. The method relies on defining the time at which testing begins, defining the number of times the valve can be closed and opened, and determining the acceptable extent of pressure rise.
Manometric temperature measurement utilizes the data from pressure rise testing to calculate product temperature, vapor pressure of the ice at the sublimation front, and the resistance to mass transfer (Rp). Programs are available on some laboratory-scale lyophilizers, such as the SMART freeze-dryer that uses an algorithm to manipulate the setpoint shelf temperature to maintain the desired product temperature.4 This method automatically determines the endpoint of primary drying while using the most efficient processing conditions.
ALTERNATIVE METHODS OF PROCESS MONITORING
Tunable Diode Laser Absorption Spectroscopy (TDLAS) optically measures the mass flux of water vapor from the product chamber to the condenser. TDLAS is an instrument and method developed by Physical Sciences Inc.5 The measurement is made using sensors and detectors that are attached to the spool piece of the lyophilizer (Figure 5).
The water vapor concentration and gas velocity data are used to solve equations for the first principles of heat and mass transfer.
Where dq/dt is the heat flux in calories per square centimeter, Kv is the vial heat transfer coefficient, Av is the area of the outside of the vial, Ts is the temperature of the shelf surface, Tb is the temperature of the product in contact with the bottom of the vial, dm/dt is the mass flux in grams per hour per square centimeter, and ΔHs is the heat of sublimation of ice (670 calories per gram).
Resistance to mass transfer of the dried product layer is also done using TDLAS and the following equation:
Where Ap is the cross sectional area of the product (the area of the inner diameter of the vial), Pi is the vapor pressure of ice at the sublimation front, and Pc is the chamber pressure. We base design space calculations on the resistance of the dried layer at the end of primary drying, since this represents a maximum value. Thermocouples are placed in the bottom of the vial and, as the sublimation front approaches the bottom, the measured temperature closely approaches the temperature of the sublimation front. The vapor pressure, Pi, is calculated from the product temperature using the following relationship:
Where Tb is the temperature at the bottom of the frozen layer.
The aforementioned equations are used in combination with values of Kv, Rp, and the maximum, allowable product temperature to construct the design space (Figure 6). Note there are two types of temperature isotherms – shelf temperature and product temperature. The product temperature above which the product fails becomes a boundary of the design space. The other boundary is equipment capability, since every freeze-dryer has a maximum sublimation rate that it will support. Another method of collecting data to solve the equations for the first principles of heat and mass transfer is using a heat flux sensor developed by Millrock Technology.6 The heat flux sensor is located on a shelf of a lyophilizer, and vials are placed directly on the sensor (Figure 7). The sensor directly measures heat flow from the shelf to the vial to obtain Kv for the vial and calculates Rp using the data collected using the sensor.
Finally, mass spectrometers, such as residual gas analyzers, can be attached to lyophilizers to monitor materials flowing from the product chamber to the condenser. This can be used to detect water vapor to determine the endpoint of primary drying, but it is quite useful for monitoring the removal of organic solvents that may be used in a formulation, monitoring for leaks of silicone from the equipment and monitoring for leaks that can lead to a loss of sterility assurance.
SUMMARY
Multiple methods are available for process monitoring during freeze-drying. The methods are useful for assessing challenges that may occur, but they are even more useful for detecting the endpoint of primary drying and for improving the efficiency of a freeze-drying cycle. Comparative pressure measurement is an easy and inexpensive method for monitoring primary drying that poses no risk to sterility assurance unlike product thermocouples. Advanced methods are available for monitoring mass flux and heat flux to solve for the first principles of heat and mass transfer equations. Solving the equations can support the development of a process design space and improve the understanding of conditions that can lead to product failure during primary drying.
REFERENCES
- Gandhi, T., 15.4.1 Thermal Simulation Model, in Microelectronics Failure Analysis Desk Reference (7th Edition), ASM International.
- Lipták, B.l.G. and K. Venczel, 4.15.3 Thermocouple Types, in Instrument and Automation Engineers’ Handbook (5th Edition), Volume 1 – Measurement and Safety, Taylor & Francis.
- Tempris. Tempris Sensor Technology Brochure. [cited 2020 March 25]; Available from: https://www.tempris.com/wpcontent/uploads/2015/04/tempris_brochure.pdf.
- Scientific, S. SMART Freeze Drying. [cited 2020 March 30]; Available from:https://www.spscientific.com/Products/Freeze_Dryers_/_Lyophilizers/FTS_Systems/Floor_Model_Tray/Pilot_Lyophilizers/SMART_Freeze_Drying/.
- Inc., P.S. LYOFLUX: Tunable Diode Laser Absorption Spectroscopy. [cited 2020 March 30]; Available from: http://www.psicorp.com/casestudies/lyoflux%E2%84%A2-tunablediode-laser-absorption-spectroscopy.
- Inc., M.T. AccuFlux Heat Flux Monitor & Control. [cited 2020 March 30]; Available from: https://www.millrocktech.com/accuflux-heat-flux-monitorand-control/.
To view this issue and all back issues online, please visit www.drug-dev.com.
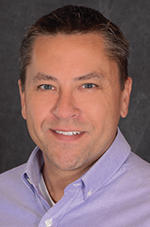
Dr. Gregory A. Sacha is a Senior Research Scientist in the Research and Development department at Baxter Healthcare in Bloomington, IN. He is responsible for the formulation and process development of parenteral dosage forms that include both large and small molecules. His work resulted in several patents for formulation and process development of large molecules. His interests and expertise are in lyophilization and thermal characterization of pharmaceutical products. Dr. Sacha developed and leads a workshop for the study of formulation and process development for lyophilized products in collaboration with the McCrone Group and Millrock Technology.
Total Page Views: 15642